このページには、一部にPDFファイルを利用しておりますので、閲覧にはAdobe readerなどの閲覧アプリが必要です。
木工関連
木工旋盤もどき その1
2016.9.24
平行してアイデア出ししていた『木工旋盤もどき』の図面をアップします。
AR-2のボディと脚部を想定して、1200x450のサイズにしました。
もう少し大きくても良いとは思いますが、あまり大きいと強度的にも難しくなりますし、それ以前に収納に困ります。
それぞれボディ、脚部をチャックした状態は以下のようになります。
使用する主な部品としては、
1.単相モーター200W EFOU-KR 200W
2.菱形ベアリング LF203
3.VプーリーA形 VP2-1/2XA1D14
4.ブッシングプーリー SPA-90-1 + SP1210x12
などになります。
減速比が小さいので、モーターの速度制御が必要になります。
間違ってAC単相進相コンデンサ付きのモーターを購入したため、速度可変制御にはDCモーターのように電圧制御でなく周波数制御が必要になりますが、3相モーターと違いインバータ位相制御では上手くいかないのが分かっているため設計に立ち向かう一歩が踏み出せないのも事実です。
こちらも材料は入手済みですが、残念ながら作る時間がありません。
ボール盤冶具製作 その2 LD照準器
2016.9.22
少し時間が取れたので前回設計の見直しをしたところ、DIY店などの市場流通材料を使うなどして簡易化が可能なことが分かりました。以下にツラツラ記してみます。
まず、LDの躯体部分ですが、□15mmのアルミ中空角棒と手持ちのt1.5mmアルミ板を使って作る事にしました。これによりコスト的には従来の半分近くまで削れます。
元の設計は長時間使用を想定したため、LDの寿命を少しでも延ばす為に放熱を考えてアルミ無垢材から切り出すようにしたので、それなりのコストがかかっていました・・・懲りないコリ性なので・・・。
次に取り付けアーム部分ですが、やたら山谷の曲げが多く作りにくいものでしたので、かなり構造を簡略化しました。それでも構造強度的には落ちていないと思います。
早く作りたくて、ウズウズしているのですが、なにぶんにも時間が無いものでして・・・。
ボール盤冶具製作 その1 LD照準器
2016.9.4
約4ヶ月のブランクがありましたが、生活も落ち着き始め、少し時間がとれたので、大物ではなく「AR-2製作のための冶具作り」を進めることにしました。
私のようなシロウトがボール盤を使う上で、いつも困るのが「ドリル刃の先端を対象物の穴開け中心位置に正しく設定できない」ということです。(ポンチ打ちをして中心を明確にしても思うように上手くいきません)
刃を回転させて切削を開始する前に、対象物に付けたポンチ穴の上にドリル刃が接するようにしながら対象物の位置を合わせます。(たぶん、みささんも同じ動作をすると思います)
この動作のときにドリル刃の先端が良く見えなくて、中心に合っているのか不安なままに、いざ回転させて穴を開けようとすると・・・刃が一瞬ブレて予定していない位置に穴が・・・。
確かに、安物のボール盤に付いているチャックは芯出し精度が悪く、ドリル刃が若干偏芯して回転しているために正確な作業を阻害していることもありますが、それ以前の問題です。
先日、加工機器のサイトをネットサーフィンしていたところ、ドリルチャック換装の記事(http://arara.amamin.jp/e565424.html)を見つけました。良いチャックが欲しいな〜と思いながら読み進めていくとLD(レーザーダイオード)のクロスライン照準器の記述を見つけました。
クロスライン照準器については、以前、ネット通販で探したことがありましたが、これと言った市販品が見つかりませんでした。多分、取り付けが機器により異なるため汎用としての販売が難しいのでしょう。
このブログの作者も同様の思いから自作することにしたようです。
まず、LD素子についてですが、私自身、数十年前の学生時代に学んだザックリした知識(コヒーレントの高い光だという程度)しかなかったので、まずはこの部分からネットで探してみました。
正直、LEDは仕事で使っていたので設計はお手の物(私の設計した民生機器でLEDの無いものは皆無でしたし、電流と輝度、放射パターンなどの定型設計で十分足りた)でしたが、LDについてはCDやDVDの駆動ユニットをブラックボックス的に扱っていただけですので素子としての知識は殆んどありませんでした。
大手メーカーのHPを中心に素子の情報を調べましたが、出力特性を見る限り電流制限をキチンとしないと直ぐに熱で壊れそうです。
(図1:長時間の使用は寿命にも影響がありそうです)
実際には励起レーザー発振を開始するとエネルギー変換効率が上がるので傾きdP/dIが大きくなりますが、出力の制御が難しいだけで電流が極端に大きくなる訳ではありませんので杞憂かもしれません。
ただ、半導体なのでトランジスタのように熱暴走することも考えられます。
メーカー製のLDは安定動作を最優先としているため、FB制御を基本と考えているようです。
したがって3端子構造となっているものが多く、LDの入出力端子以外にPD(出力検出用のフォトダイオード)端子が付いています。
LDの出力をモジュール内部に設置したPDでモニターするようになっていて、外部でFBをかけて安定化させるためのものです。
これもWeb検索していて見つけたのですが、ELM185XBを使った制御例がありました。(図2)
今回購入したLDモジュールは安モノですので入出力の2端子のみです。(シードスタイル レーザーラインユニット ストレートタイプ @980)
したがって外部で定電流回路を組まねばなりませんのでLM317を使って定電流回路を組む事にします。(図3)
LM317はOUT端子とADJ端子の間が1.25Vになるように制御されるので、抵抗R1を流れる電流は
I = 1.25/R1
発振開始電流が不明ですが、おおむね75mAあたりと考え、動作電流を100mAに設定すると、R=12.5Ωとなります。
抵抗での消費電力はP=I2xR≒0.13Wですので1/4W抵抗でOKです。抵抗での降圧は1.25VですのでLDのVfが約2VとしてVout≒3.3V
LM317Tのロスを考慮してもVinが5.5V以上あれば動作は安定するでしょう。
機構設計については、以下のように進めます。
LDモジュールは放熱を考慮しているのか、LDポインター実装用のためなのか、φ9xL20の真鍮製ケースに入っていますが、その外側をアルミ躯体で覆い、ヒートシンク兼用とします。(図4)
レーザー放射パターンはライン状ですが照準器として使うには極めて太いため、アルミ躯体の放射面にスリット構造を設けて絞り込みます。
LM317と電池ホルダー等はアルミ製の別筐体に組み込み、撚りリード線でLDに給電する形態とします。
ドリル刃を上下させてもレーザークロスの交点が移動しない条件は、『レーザー発光パターン(ライン)を垂直に床面に当てた場合にその延長線上にドリル刃のターゲットがあること』となります。
こうすれば、発光パターンは延長線上を移動しますがターゲットを外れることはありません。(図5〜7)
直交するY軸方向でも上記の条件を守ればターゲットを通る延長線上にパターンを形成することができます。
機構部分については、ざっくりと構想を固めてから設計に入りました。
私が使っているボール盤は、藤原産業製の卓上ボール盤SDP-300Vですが、オーソドックスな作りで可動部がコンパクトに作られています。
可動部がコンパクトに作られていて手元の自由度が高く材料加工スペースの見通しが良いというメリットの反面、取り付け構造に困ることが想定されました。
可動部の上下駆動レバーが本体の右側にある(工作機械にも右利き文化が浸透している)ので、1個は右横から照射し、もう一方を後方0度から照射(+字形クロス)にするか、2個とも後方45度から照射(X字形クロス)にするかの選択に迷いましたが、後者を選択しました。
どちらでも良いのですが、理由は単純で、後方0度からの照射が直接目に入りそうな気がしたからです。
LDの支持部分と電源ケースは強度より加工性を優先しアルミ製とします。可動部の上下によって、どの程度パターンが移動するのかシミュレーションだけでは分からないので、LD格納部と支持部との間は角度調整ができるような構造とします。
図8に示すようにセンターポールと可動部の間にちょっとした窪みがあり、ここに電源部分を収めるのが合理的です。
ここまでの構想を元に設計をした結果が以下になります。
LD取り付け部は図9のリングアダプタを基準に設計しました。
板厚は1.5mm。展開図から折り曲げて作りますが、強度を稼ぐためにLD保持部分は2枚重ねとしています。
ざっくりの設計ですので、間違いがあるかもしれません。
直ぐにでも作りたいところですが、残念ながら製作編は未定です。
ルーターテーブルのベース構造について
- PDFファイル ルーターテーブル用ベースのアイデア
2016.4.29
今日は祭日。花粉も収まってきたし、朝から久しぶりの好天なので屋外で円切抜き冶具の加工作業を続けました。もう少しで完成です。
冶具の製作記は、途中経過の写真も撮らなかったし、今回はパスすることにします。
花粉で作業ができなかった間、色々とアイデアスケッチめいたものを作りましたが、今回はRP2301FCをルーターテーブルに組み込む時のアイデアを紹介します。
まずベースの大きさですが、450mmx600mmとちょっと大きめです。
これは、大型のワークを乗せた時にベースのエッジにワークの端部が引っかからないようにということも理由の一つですが、RP2301FC自体が大きいということが第一の理由です。
材質は、人造大理石(t10)+アルミ板(t1.5)を想定しています。
ルーターなどのアイデア商品で知る人ぞ知るMIRAIの「トリマ天板セット」のアイデアをパクらせていただいて、ルーターはサブベース(アルミ t6)に取り付け、ビット径に応じて2個のベース穴(φ18/φ32)を使い分けるようにしてあります。
また、私の場合には円切抜き作業が多いので、冶具をベースに組み込んでしまいました。外径は80〜400mm、内径は104〜424mmまで切り抜きが出来ます。この構造のために表面材としてアルミt1.5(ステンレス製スケールの厚さに合わせる)を使う設計になりました。ステンレスの直スケールが表面と面一になるようにしています。
RP2301FCの場合には、テーブルにマウントした場合に天面からビットの突出量を可変できるような他社に無い独自構造を持っていますが、サブベースと組み合わせた場合、構造的に40mmの長穴になるので強度的に心配です。この部分に関しては、まだ、良いアイデアが浮かびません。
そして、これが一番使い勝手に効いてくると思いますが、ビットの交換を簡便にするために、昔のミシンの収納方式をヒントにした片ヒンジでベースを持ち上げる構造を取り入れました。
最終的には集塵ホースを収納したフェンスを円切抜き冶具のある部分に設置する予定です。この部分にも独自のアイデアを盛り込みたいと思っています
コレットチャックの仕組み
- PDFファイル コレットチャックの構造
2016.4.22
ドリルやルーターのビットを回転軸(スピンドル)の中心に固定する部分をコレットチャックと呼びます。
コレット(collet)の意味を辞書で調べたところ、旋盤で筒状の部材(ワークの事か・・・)を固定するために用いられるコーン形のつかみ(チャック)という説明がありました。
A cone-shaped chuck used for holding cylindrical pieces in a lathe.
また別の意味として「宝石などの台座の爪」というものもありました。中世の貴族服の縦ギャザーの入った「立て襟」もスペルは異なりますがコレット(Collette:フランス語?)と呼ぶようです。形状が似ている?ので、旋盤のチャック部分の名称に使われたのかも・・・意訳としては「固定対象を周囲から均等にホールドするためにスリ割りの入ったコーン形状のもの」というところでしょうか。コレットコーンという名称も現存しています。
旋盤のチャックというと、爪を使って回転軸にさまざまな径のワークを固定するものをさすことがが多いと思います。コレットの場合には、爪ではなく数箇所に縦スリットの入った円筒でワークを締め付けるように固定する構造なので接触面が多く取れ、負荷がかかっても保持力を求められるドリルビットやルータービット、フライス盤用エンドミルの固定に使われます。
購入したムック本にはビットの底突きに対する注意書きがありましたが、説明図も含めて何となく合点がいきません。
そこで自分なりに調べてみた結果が以下の内容になります。
文字が小さく見辛い場合には、キーボードの『Ctrl』ボタンを押しながらマウスのスクロールダイヤルで画面の拡大率を変えるか、以下のPDFをご覧ください。
ビットの種類と用途について
- PDFファイル ビットの種類とその用途
2016.3.27
相変わらず花粉全盛ですが、いつまでも部屋でくすぶっているのも業腹です。
2週間前から円切抜き冶具の製作を続けてきました。先週、発泡塩ビシートが不足していることを報告しましたが、実は、円切抜き冶具も影響を受けました。
代用品としては意外と強度があるMDF(Medium Density Fiberboard)を使うことにして、近くのDIY店を物色。3mmは無く、4mm、9mm、12mmのステップしかありません。
仕方なく4mmを購入し、再設計。アルミ板は1.5mmを2枚貼り合せるのは変わりません。
昨日はMDFのカットと一部貼り合わせ。今日はアルミのカット。花粉混じりの風と戦いながら、マスクをかけての作業・・・おかげで目は充血し、痒くて痒くて・・・(≧▽≦)
3時くらいにはギブアップして室内に引き上げました。
ルーターを購入してから正しい使い方を求めてずいぶんとWEBサーフしましたが、ビットの種類や、それに適した使い方などをキチンと説明してくれているサイトに行き当たりません。
唯一、ムック本で学研の『新 トリマー&ルーターテクニック』をAmazonで見つけ、早速入手しました。良くまとまった本ですが、残念ながら情報が散漫です。仕方ないので、色々なページからかき集めた情報を一覧表にまとめました。
自分で使うための資料なので、必要な情報しか入れていません。
ご参考まで。
ちょっと休憩
2016.3.6
花粉が本格的に飛び出しました。
月曜から金曜までは出勤しなければならないので、帰る頃にはマスクをかけていてもグズグズ状態で、保護できない目は涙目になっている今日この頃です。
反動から週末は外出を避ける事になりますが、昨日は法事で千葉と茨城の県境近くまで遠出・・・帰る頃には・・・。
今日は、昨日の疲れもあって、室内でダラダラ・・・ルーターを扱っているWebを見たり、オーディオ関係の資料を見たりして過ごしました。
そんな中で、室内で使用するスピーカーキャビネット用塗装ブースの記事を見つけました。
不織布を使った衣装ケースを利用することで安価にできることをメリットに挙げたもので、アイデアはすばらしいと思います。
しかし、気になったのは塗装とサンディングを同じ場所で行うという部分で、残念ながら、これは『ミソクソ一緒』の典型です。
どんなにきれいに掃除しても、繰り返し使用するうちにサンディングによる微粒粉は残り、塗装作業の際に舞い上がり、塗膜表面に付着します。
この記事を書かれた方もご自分で作業していて気が付かれると思いますが、塗装はホコリの無い環境でないと満足できる仕上がりは期待できません。
分けることができないのであれば、どちらかの作業・・・サンディング作業は、ご自宅の庭か、近くのホームセンターに開放作業場があれば、そこを使わせていただくのが一つの方法です。(材料購入を条件に作業場を開放していただける店舗が増えてきています。ただし塗装は不可!)
当然ながら、電動サンダーを使うとダストが舞い上がり周囲に迷惑をかけますので手作業が原則ですし、周囲に他の作業者がいないとしても2〜3mは飛び散るので作業後の作業場清掃はマナー上マストです。
木工製品の塗装は、下地処理が7割、塗装作業が1割。残りが乾燥と塗装の専門家にお聞きしました。
「木口を砥の粉で埋めないと塗料を吸い込んでしまい、必ず凹凸ができてしまう」とか「穴や凹みの修正でパテを使った場合、十分乾燥させないと塗料の内側に水分が残り、曇りが出たり剥がれたりする」など、下地処理で仕上がりが決まるのは理解できていましたし、塗装時にホコリが表面に付着した場合には、乾燥後に完全には修復できないのも、痛いほど経験していました。
乾燥が重要だというのは、専門家から話を聞くまでは分かりませんでした。乾燥は、どのように実行しても水分や有機溶剤がキュァすれば良いとばかり思っていました。
専門家曰く、従来からあるワニスなどのエマルジョン系塗料(2液を混ぜて重合反応するウレタン系やエポキシ系、空気と触れて酸化反応で硬化するもの以外のもの:物性が化学的に変化しない)の場合には融着乾燥というメカニズムが起こるそうで、その場合には「最適な温度と湿度がある」とのこと。
基本的には、「湿度が低く一定の温度が続くのが良い」とのことでした。
彼は有機化学を学んだ経験から、なぜその条件が良いのかを説明してくれました。
ヒーターを用いて熱硬化する樹脂を主体とした塗料(粉体焼付け塗料)や常温でも分子どうしが共重合反応などにより硬化して非常に硬い塗膜を形成するものとは違い、エマルジョン系の場合、塗装直後の塗膜の中では溶剤の中に塗料の粒子が漂っている状況で、徐々に溶剤や水分が表面から気中に放出され、塗料粒子どうしが規則正しく法則に則って弱く結びつき始めるのだそうです。
表面から放出される速度は周囲の湿度に依存するので、乾燥していれば表面から均一に結合が始まり、その隙間を縫ってその下にある溶剤が放出されます。順次、表面より固まっていき、最後に下地まで固まります。
湿度が高く表面の溶剤がなかなかキュァしない状況だと、内部の溶剤がなかなか放出されないばかりか表面の粒子結合が弱く、距離的に近い部分から「塊り」になり、縮みやシワ、曇りなどが発生しやすくなるそうです。
最悪の場合には、不均一な結合が原因で応力歪みが生じ、ヒビが入ることもあるとか・・。また、赤外線ヒーターなどで急激に温度を上げると下地に近い部分からの放出が早まり、且つ、表面の結合が異常に早くなるため気泡ができたりするそうです。
彼曰く、「塗膜は生き物」だそうで、最初の育て方でその後が決まるそうです。
ヴァイオリンに塗ったニスも然り。ストラディバリやアマティの時代、ニスの塗り方や乾燥工程をノウハウとして守ったからこそ、200年以上も良い状態が維持できたし、その後の保存する環境が良かったから未だにすばらしい音を紡ぎ出しているというのが彼の持論です。
いずれにしても、塗装にもノウハウがあり、ただ塗れば良いと言うものではないということですね。
AR-2では、黒のピアノ塗装に挑戦するつもりです。
テンプレーターの設計 その2
- PDFファイル テンプレーター・ガイドの問題点
- PDFファイル テンプレーター修正版
2016.2.27
前回の記述で間違っていた部分がありました。
最近、間違い探しばかりしているようで・・・。何はともあれ、内容は次のようなものです。
「〜先端をビットの径に合わせて幅の違うものに付け替えれば、テンプレートの外形に合わせて加工ができる」という部分ですが、認識が甘く、部分的に間違っていました。
以下の図を見て下さい。
ルーターを縦に取り付けた場合のテンプレート検出部とビットの位置関係を示した図です。
左がビットの径とテンプレート検出部分の幅を合わせたものです。
左から右にトレースした場合、ビット中心とテンプレート検出部分のテンプレートに接した部分(右角)との距離差がトレースのズレになります。
テンプレートが図のように変位が一方的であれば、この距離差分テンプレートをずらすことで対処できるため問題ありませんが、変位がマイナス(傾きが逆)になると検出部の左角がテンプレートと接するようになり、距離差も逆方向に発生します。
ということは、傾斜が逆になると距離差x2(ビット直径に相当)だけ加工がずれるということになります。結果的に、形をコピーする雛形というテンプレートの意味がなくなります。
ルーターを縦に取り付けた場合、テンプレートと接する部分は出来る限り「点」にすべき・・という結論に至りました。(右側の図)
現実問題として、点ではテンプレートにスムーズに当てることができないので、先端部を小さなローラー(ベアリング)にします。
ローラーのRより小さなRの変位には対応しませんが、面をローラーがトレースできる状況では点接触になるため、距離差の問題はクリアできるはずです。
ルーターを横に寝かせて取り付けた場合(ろくろと組み合わせて外形削りをする場合)には下図のようになります。
この場合には、傾斜がプラスからマイナスになってもテンプレートとの接触部の幅がビット径と同じであれば、距離差は出ないことが分かります。
詳細は、PDFファイルを参照してください。
現時点での構造図は以下のとおりです。
今日は、もうひとつの趣味である写真の祭典『CP+』に行ってきました。
進化を一番感じたのは、誰でもキレイな写真を撮れるのは当たり前の時代が来たということ。ピンぼけはありえなくなりつつあります。ピント位置をずらして数枚をブランケット撮影してカメラの中で合成することで短焦点のレンズでも被写界深度を考えなくても良いのです。
今までの常識が通じない写真がディスプレイに表示されているのを見ると、ここまで来たのか・・という感じです。ただ、スムーズにピントがボケていく表現ではなく、奥行きを部分的に圧縮したような不自然な感じを受けました。
これもデジタルに移行して銀塩の粒状感が無くなった感覚に似ていて、いつのまにか当たり前になってしまうのでしょうね。わざわざ粒状の感じを出す効果を盛り込んだ製品も出てきていますし・・。
それと、写真は撮る〜見る〜プリントするという行為だけでなく、それを簡単にその場で共有(シェア)できる方法がどんどん増えてきていることを感じました。
TransfarJet対応SDHCカードもそのひとつ。スマホへの転送は自由自在ですし、PCやプリンタへもSDカードを差し替える必要なく転送できるのです。
報道写真もシロウトの映像がテレビなどで再生される昨今ですので、方向性としては当たり前といえばそれまでですが、ここまできたか・・・という感じです。
動画も4Kは当たり前で、CANONでは8K動画のデモンストレーションをしていましたので行列に並んで体験。NHK技研で数年前に見て以来でした。慣れとは恐ろしいもので、2Kから4Kになったときの感動に比べて4Kより4倍精細な8Kなのにイマイチと感じてしまいました。
それでも大画面でのアラは気にならないレベルだし、画像処理が上手くなってきているのを感じます。私が携わっていた10数年前は「動きの無い部分の記録情報量を減らす」というMPEGの処理が不自然でしたが、殆ど不自然さを感じなくなってきています。
奥行き感もハンパ無いので、不自然な3Dは必要ないと感じました。
16Kのホログラムなんていうのも20年以内には可能なのではないでしょうか。そうなってくると、擬似空間のクオリティも上がるのでしょうね。夢は広がります。
せっかくカメラを抱えて横浜まできたのだからと、赤レンガ方向に歩きながら撮影。象の鼻から街中に向かい、横浜税関や県庁、開港記念館などを撮りながら桜木町に戻る途中、馬車道の勝烈庵本店でカツレツ定食の昼食。鎌倉や横浜地下街にも勝烈庵があるけれど、やはり本店の揚げ方が最高!ご飯2杯半とキャベツお代わりで満腹。満足して帰宅したのは午後3時前。
そんなこんなで、午後から円切抜き冶具を作ろうと思っていましたが、疲れて挫折。明日は頑張ろう。
テンプレーターの設計
- PDFファイル テンプレーター
2016.2.14
今週末は荒天なのを良い事に、作業より設計を優先させました。
円切抜き用冶具の致命的欠陥については、なぜこんな単純な事に気付かなかったのかと自分の老化を呪いました。
思い込みが強くなり、頭が固くなっているのでしょう。
「でも、大きな径なら使えるんでしょ」と長男が言ってくれたのが唯一の救いでした。
昨日の土曜日は、各パーツの設計見直しを行い(例によって、早とちりや勘違いによる設計見直しもありました)、使用するラック&ピニオンを決め、発注するだけにしました。
ちょっと遡りますが、2/11(木)にはMJ誌主催のオーディオフェスティバル(秋葉原・損保会館)に出向き、金田明彦さんや小澤隆久さんの姿、そして団塊の世代の方々、そしてもっとお年を召した方々の熱気に触れてきました。
開場直後の11時過ぎに入場したのですが、それなりに盛況だったので席は殆ど埋まり、音を真剣に聴く環境でもありませんでしたし、展示説明にしても万人向けの内容になりますので、掘り下げができるはずもありません。文字通り『フェスティバル』で雰囲気を楽しむためのものです。
それでも、金田さん製作の電流伝送ハイブリッド真空管アンプの音出しでは、半導体だけのアンプでは出せない低音の雰囲気が味わえました。
1時間ほどで切り上げて、遠回りしてコイズミ無線を冷やかして駅まで帰ってくるコースを選びました。
街には電気製品以外を目当てにした若い人たちが溢れていて、立ち食い焼肉の店もできていてA5クラスの肉をリーズナブルに食べられるからか行列ができていました。
AKB48目当ての若者も相変わらず多く、駅近くにはAKBカフェの隣にガンダムカフェなんぞもできていて(前からあって、私が気がつかなかっただけかも・・)、びっくりぽんでした。
フラフラと誘われるように、唯一、昔の秋葉原を感じさせるラジオセンターの路地も通ってみましたが、人通りはまばら・・・。なじみの「小沼」でAR-2用のSP端子を購入しました。
色んな意味で、たまには東京も良いですね。
今日も荒天が続いているので、テンプレーターの設計・・・といっても構想は固まっていたので、図面に起こしただけですが・・・を進めました。
X-Yのフリーテーブルで可動域が580mmx200mmのものです。
「テンプレートガイド」の先端をビットの径に合わせて幅の違うものに付け替えれば、テンプレートの外形に合わせて加工ができるというものです。
「セットカラー」は、X軸、Y軸をそれぞれ意図した位置に固定することができるように設けてあり、ルーターの取り付け位置を90度変えることで加工のバリエーションを広げられます。
別途、『ろくろ』構造も考えていて、これと組み合わせることで、テンプレートを使ったAR-2の量産も想定しています。
天気が回復したので、外の空気を吸いに行ってきます。
花粉症なので、マスクを付けての外出ですが・・・。
円切抜き用冶具の致命的欠陥について
- PDFファイル 冶具再設計
2016.2.12
せっかく作った冶具ですが、致命的欠陥があることに気付いてしまいました。
一番半径の小さな位置まで可動部を移動しても、φ200mm以下の円がトレースできないのです。
実際には12mmのビットを使えばφ190までは可能となりますが、残念ながらフローターの加工には使えないということです。
そこで方式を完全に変更します。
既存のボトムプレートを外して、その代わりに装着する方式にします。
早速、構造を調べるためにボトムプレートを外してダイキャスト部分を剥き出しにしてみました。
ダイキャスト部分にはリブが走っているため、プレートの下に中心軸がくる場合の「逃げ」は無いようです。
そうなると、円加工のための中心軸はボトムプレートの厚さ分の保持しか期待できないことになります。
元々、ベアリングに固定したφ8のシャフトをM10のボルトの頭に穴を開けたものに差し込んで中心軸を構成するつもりでしたので、この部分に関しては小変更です。(ベアリングや冶具ボルトを使える寸法はありませんが・・・)
再々設計したものは、このようになりました。(詳細はPDFを参照してください)
スライド板に50mmピッチで開けたφ8穴を切り換えることで、外形抜きなら最小径はφ80−ビット半径、最大径はφ550mm−ビット半径くらいまではいけそうです。
径の変更は、望遠鏡の接眼部の駆動に使われているラック&ピニオンを利用しました。
スライド板の固定は、側面よりピニオンギアの軸を押さえる事で行います。
この時に問題となるバックラッシュは、遊びをコントロールしてグリスアップすることで、問題ないレベルに抑えられると思います。(固定するときにピニオンをラックに押し付ける方向なのも一役かっています)
ラック&ピニオンは、小原歯車工業のSRラックSR1-100と平歯車SS1-29(ともにモジュール=1)を選定しました。
モノタロウで確認しましたが、ペアで1200円ほどです。
今日は、設計までで根が尽きました。
円切抜き用冶具の製作 その2
- PDFファイル 円切抜き冶具 浮き上がり
2016.1.24
セメダインの『エポキシパテ金属用』を購入しました。
粘土状のものを必要なだけ切り取り、指で良く練って色が均一になれば反応が開始して硬化が始まります。
全ねじの溝に指で塗りこんでいきます。気温が低いからか、練っても柔らかくならず、指で溝を埋めるのには力が要ります。
3〜4分以内に作業を終わらないと硬化してしまいます。気温が低いから5分くらいは大丈夫だろうと高を括っていたら、硬化して作業ができなくなったので、二度目からは量を少なくして規定時間内に作業を終えるようにしました。
最初は溝が埋まるくらいの量を均一に広げようと努力しましたが、作業半ばで親指が痛くなり水ぶくれができてしまいました。これ以上、指を酷使できず、途中からは厚めに塗り広げて、後からヤスリで削るよう方針を変えました。
10分くらいすると最初に埋めた部分はカチカチになります。
慣れてきたので30分程で表面をパテで覆い終わり、完全硬化を待つことにします。
約2時間後、ヤスリがけを行いますが、かなり硬度が高く、コンクリートを削る感じです。
完成したものがこれです。
ねじ全体が白っぽいのはパテが溝に残っているからです。ヤスリで山が出るまで削ったので、写真では溝があるように見えますが、光っているのは『ねじ山』です。
削り終わり、表面を触ってみると、山は確認できるものの、引っかかる程ではないように思えました。
いざ、可動部を差し込んでみると、まだ引っかかる感じが・・・金属同士の表面が引っかかる感じです。
近くにあった切削油を軽く表面に馴染ませてやると、スルスルと動き始めました。ホッと胸を撫で下ろします。
早速、ルーターに取り付けてみました。
冶具の下面は床面から3.5mmくらい浮く設計ですが、実測すると5mm以上あります。
原因を調べてみると、ルーターがシャフトを固定するねじ(上の写真内矢印)はガイドホルダを固定する目的に適合させるために今回の冶具とは反対側に位置しているので、固定位置からのスパンが長くなり浮き上がっているようです。因みに固定ねじを緩めると3.5〜4mmになりました。
浮き上がりを防止する方法を考えないといけませんね・・冶具に近い側でシャフトを下に押し付けることができればOKだと思います。シャフトの上面にスペーサーを設定するのが常道です。
今週は時間切れ。来週の作業にします。
作業台の製作 その3
- PDFファイル 作業台寸法(2分割) 図のGの部材を天板(ベース)に取り付ける際には、先に脚部の指定位置(脚部の上面とGが面になるよう)にGを木工用クランプで固定して、貫通穴を開けます。
2016.1.23
ようやくレールが到着。
アトムリビングテックの下部レールAFD-110 2.7mというものですが、MonotaROの在庫が無かったらしく、流通品を探していたのか?それとも新規に押し出しを依頼した?のでしょうか、納品まで3週間近くかかりました。
これには私のミスでの遅延もありました。(住所の番地入力を間違えていました・・汗)
さっそく、今日は午前中からこのレールのカットを行い、作業台の組み立てに取り掛かりました。
組み立ては、2分割にするよう構造を変えたので、まず天板部分と脚部を繋ぐ部分を組み立てます。
3/8インチのウィット規格の半ねじで固定してクランプを外し、天板(ベース)を乗せてコーススレッドでベースとGを固定します。この際、バラした後の組み付けがスムーズにできるように、片側だけGと脚部の間にコピー用紙を挟みます。
ほんの数十ミクロンの隙間ですが、やるとやらないでは大違い。
以前、同じ方法で組んだ際にバラすことができなくなり、木槌で無理やり外して接触する面に均等にヤスリがけをすることになり、大変な思いをしました。
固定後にベースを外し、紙を外して乗せてみると、殆どガタ無しでスムーズに挿入できます。箱根の組子細工のようで気持ちが良いです。(自画自賛・・)
あまり隙間を開けてしまうと半ねじを締めこんだときに歪みますし、コピー用紙1枚〜2枚がベストです。

この時のコツとしては、クランプ冶具を可能な限り使って、ベースとトップの隙間を作らないようにすることです。
分割したそれぞれのトップがレールを挟み込むような構造になっているので、レールに加工ツールを固定したときにはトップとベースに剥がれる方向の力が加わるからです。
1枚ずつトップを貼っていき、完成したものが、このようになりました。

接着剤が乾く間に、脚部に『滑り止め付き安対アジャスタ 標準タイプ AJSH8』というものを鬼目ナットを使って4箇所に取り付けます。
4箇所に増やしたのは、『トップの水平を出すことが必要な場合もあるだろう』と考えたからです。
通常の作業でも、水平が出ているに越したことはありません。どこかに水準器を組み込まねば・・。
AJSH8の床と接する部分には、滑り止めの樹脂が入っていますが、組み立て作業の際にキズが付いてしまいました。
作業場所が駐車場になるので、仕方が無いですね・・。

それぞれ天板部分と脚部が組み終わりました。

組み立てると、このようになります。

あとは、実際の作業に使ってみるだけです。
明日は、円切抜き冶具のシャフトをエポキシボンドで埋めることにします。
お疲れさまでした。
円切抜き用冶具の製作
- PDFファイル 円切抜き冶具-1
- PDFファイル 円切抜き冶具-2
2016.1.17
昨日は、早々に冶具設計に着手。午後早い時間には図面を完成し、部材を調達するために颯爽とDIY店に向かったのですが・・前途多難・・。
当初、構造は以下のようなものでした。
2本のスライド棒の直径および幅をルータ添付のガイドホルダと同じφ11、幅ピッチ115mmにして固定方法を共通にしたものです。
こうすれば、ベースの加工をすることなく、アタッチメントを交換するようにして円切抜き冶具が付けられます。
売り場で、まずφ11のステンレス丸棒を探しましたが、ありません。最大でφ8まで・・。それでは、パイプならあるだろうと売り場に行くと、何と!φ9.5の上はφ13になってしまう・・確かにφ11という寸法は標準とは思えないですね・・。
即、発想の転換・・それに変わる材料はないかと探したところ、M12の全ねじが見つかりました。
これであれば、径は約φ11あたり・・溝を埋めれば何とかなるはず。
1m品が主流のようですが、カットには時間がかかるので長さの短いものを探すと、ちょうど285mmのものがありましたので、これを流用する事に決めました。
次は、スライダーとエンド部分の□20mmの真鍮材を探しますが、角ブロックさえありません・・。
□10mm以上の外形で、置いてあるのはアルミの角パイプだけ。□15mmと□20mm。使えそうなのは、□15mmだけ。
でも、材料の厚さがt1.5mm・・・果たして、ねじが切れるか・・?
蝶ねじは力がかかるのでM6で設計していましたが、t1.5では2山切れない・・。諦めて、すべてをM4に変更しました。これでも2山がやっと・・。
続いてt3の梁にする材料を探しましたが、これも鉄のムク材はまったくありません・・。途方に暮れていても仕方が無いので、代用品を探します。
ありました! 建材コーナーにパワープレートという名称のものが。数箇所に丸穴や長穴が開いたもので、これをカットして使う決心をしました。
そんなこんなで、現実に作るものは以下の図面のものになりました。
パワープレートは両サイドの10mmずつを切り落とし、仕上がりで130mmとします。
可動部の中央には、ベアリングを圧入(焼き嵌め)する予定なので、店で売っている中で最大のφ13の金工用ドリル刃を購入。
パワープレートの中央には既に11x20の長円穴があるので、この穴の中央を広げることにしました。丸穴への焼き嵌めより楽なのではないかという思いも・・楽なことを求めるところにアイデアが生まれる・・屁理屈。
□15mmの角パイプの肉厚が1.5mmしかないため、パワープレートと角パイプおよびエンド部分の全ねじとの嵌合部はエポキシ接着剤の併用が必要と思います。
まず、角パイプとパワープレートのカットからスタートしました。
金属切断用の電動工具(ディスクグラインダーなど)が無いため、ブレードソウに金工用の刃を付けての手作業になります。
休み休みで約1時間の格闘の末、日暮れ前にカット作業は終わりました。3mm板金の手加工は、正直いって大変でした。


今日の作業のスタートは、パワープレートと角パイプを結合するための穴開けとタップ切りです。
M4に統一したので、下穴はφ3.3のみ。アルミパイプにタップを切りますが、当然、荒タップのみです。それでも手応えが無く、不安がつのります。何とか2山はありそうです。
結合面にエポキシ接着剤を塗って、皿ねじで締めこみますが、下手をするとねじ切ってしまうので細心の注意を怠らず作業を進めます。
可動部中央にベアリングを焼き嵌めするつもりでいましたが、φ13で穴を広げた後、ヤスリでキツメの穴に仕上げる作業で失敗し、手で簡単に嵌る状態になってしまいました。
仕方なく、エポキシ接着剤の登場です。ベアリング内部に接着剤が入ったらアウトですので、PPフィルムで目張りをして長円もろともエポキシで埋める作業を行いました。
接着剤が使用硬度まで達した後、全ねじをルーターに組み付けた状態(「ガイドレール」=「全ねじ」の幅115mmを保った状態)で、いもねじでエンド部分と可動部を仮固定し、エンド部分をエポキシ接着剤で固めます。

エンド部が固まったので、ここまできたら可動部を動かしてみたくなりましたが、想定したとおり全ねじに引っかかりスムーズに動きません。
全ねじの溝にエポキシパテを埋めてやれば、スムーズになるはずです。
パテを買い忘れたこともあり、今週の作業はここまで。
お疲れさまでした。
新しく加わった工具
2016.1.16
先週は藤原産業製の卓上ボール盤SDP-300Vが加わり、今週はマキタ製の電子ルータRP2301FCが到着しました。
徐々に作業をする環境が整ってきている感じで、気持ちが高揚してきます。
昔からルータが欲しくて欲しくてしょうがなかったのですが、懐具合と相談して、やっと決心がついて購入に至りました。
AR-1の製作時には、円形の加工は、@ジグソーで荒く切り取って、Aヤスリをかけて整形する といった具合に二段階で行っていました。
精度という点では、なかなか満足のいくものができませんでしたし、何と言っても時間がかかりました。
ルータを使ったからといっても単純にはいきません。
まず、円形切抜き用の冶具を製作します。
Webで色々探してアイデアは仕込んでありますので、今週末は、冶具図面の製作と一部加工になる予定です。
今まで何回も焦って痛い経験をしていますので、急がば回れ・・逸る気持ちを抑えてコツコツと・・。完成度を上げるためには前段階の準備が大切なことは、30年を越える技術者としての経験から肝に命じています。
将来的には、今回製作した作業テーブルにルータを固定して量産体制に対処したいのですが、今回は手持ち+冶具での作業に徹します。
まずはルータに慣れることが先決です。
新しく加わった工具の写真をアップします。
ルータは電子制御で回転速度のコントロールができるもの、将来、テーブルに固定して本格的な加工のできるものという条件で探しました。
さすがDIYの本場アメリカや欧州などの海外製には、ポーターケーブルやトリトンなど、良いものがたくさんあり、中でもトリトンのTRJ-001とは最後まで迷いました。
トリトンはオプションが充実しており、テーブルに設置したときの操作性(ビット交換の簡便性など)では一日の長がありました。
それでも、敢えてマキタを選びました。
つまらない理由なのですが、以前、海外製品でカーボンブラシの入手に手間取ったことがあったのを思い出し、国内製としました。
何はともあれ、早速、冶具の設計に取り掛かります。
作業台の製作 その2
- PDFファイル 作業台寸法(950mm修正)
2016.1.11
ボール盤が入荷したと連絡がありましたので、三連休の初日に引き取りに行き、午後から材料の穴開けを開始しました。
結局、高さは900mmの仕様としました。
当初、3/8インチのウィット規格の半ねじ(建築用で値段が安い!)を使って組み立てる仕様でしたが、近くにあるDIYの店はインチの鬼目ナットだけは扱っておらず、構造的に鬼目を使わねばならない部分だけミリねじを使うことにしました。
二日目には組み立ての下準備(鬼目ナット打ち込みや3/8ナット埋め込み&エポキシ補強)もあらかた終わったのですが、三日目だというのに肝心の天面に組み込むレールがまだ届いておらず、天板の加工ができていない状態です。
イメージだけでも味わいたかったので、とりあえず天板は乗せるだけで仮組みしてみました。写真をアップします。
組んでみると思っていたより軽かった(40kg以上を想定していましたが、たぶん、25kg〜30kg程度・・・600mmx1200mmというサイズからすれば十分重いのですが・・・)のと、組み付ける時間(初めてだからかもしれませんが、ねじが18本と多く、20分くらいかかりました)や組み立ての繰り返しによるガタの発生を避けるため、組み立てたままにするほうがベターだと考えました。
結局、構想を変更して、脚部(棚一体)と天板の2分割構造にしようと決めました。
固定のために、650mm高さ用に切り出していた足の部分を流用します。(図面の茶色部分G)
これであれば、4本のねじだけで組み立てができるので、時間的な問題もクリアできそうです。
もう一つ気が付いたのですが、作業する場所が駐車スペースなのでコンクリートの打ちっぱなしになっているため、そのままではガタが出ます。
したがって、床の高低に合わせるための構造を設けねばなりません。
後ろ(どちらが後ろ??)にはゴム足、前の2本の脚部にはスクリュー式アジャスタ付きのゴム足を付ける事にします。
そんなこんなで三連休もあっと言う間に終わってしまいました。
作業台の次は、AR-2の製作が待っています。
当分の間は、作業に明け暮れる毎週末となりそうで、嬉しい悲鳴が出そうです。
作業台の製作 その1
- PDFファイル 作業台寸法
- PDFファイル 作業台寸法(900mm)
2016.1.2
年が明けました。
元日、二日と正月気分で過ごしてしまい、既に二日の夜・・・体重計に乗るのが恐い(汗)。
何だかんだで年末ジャンボの結果もまだ見ていない始末。
ところで、初夢の定義は色々あるようですが、年越し後に初めて見た夢というのが大方の見方のようです。残念ながら、今年になってからまだ夢を見た記憶がないのですが・・・。
それはそれとして、本題に入ります。
実は、今回は手抜きで、材料の切り出しを自前でなくホームセンターに依頼しました。
天板は板厚18mmのラワンランバーコア材(サブロクx2枚)を使用し、その他の脚部等は2x4材(SPF 38mmx89mm
x3650mm x3本)を使用しました。
パインやナラなどのテーブルに加工する板も販売していましたが、ある程度の強度が確保できることを前提条件に、それを満たす限りでコストを抑えました。
寸法関係は以下のとおりです。
立位では天板の高さが900mm〜1mが人間工学的にはベストのようですが、今回は650mmとしています。これは座位も想定したためで、作業がしにくければ、脚部を作りかえることにします。
天板は二層にして20mmの溝を2本設けるようになっていて、そこに冶具の固定に使うアリ溝と同じ働きをするようなレールを設置します。
天板と両サイドの脚部、底部の棚の4つに分かれていて、ボルトで組み立てる構造にしました。
年末休みの始まった当初は、カットを依頼することで工期の短縮を狙いましたが、組み立て用のボルトを通す穴を垂直に開ける自信がなく、ボール盤を購入することになりました。
ところが、製品在庫が無く、年末で入荷も無いとの事で、結局、休みの間には作業が進められないことになり、一挙に力が抜けてしまいました。
想定外・・・というよりも計画性が無い私の性格が露呈した状況で、せっかくの休みはカットした材料が山積みの状態で終わる事になります。
今年こそ全力疾走と思っていました(毎年そう思うのです)が、先が思いやられるスタートになりました。
900mmの脚部にしたものもアップしました。(2016/1/3)
レール部分は内側にボルト&角ワッシャを自由に移動できる(使わないときにはレールから外す)ようにしてありますが、t1.5mmのアルミ押し出し材なので、固定物との間には大きめのワッシャを噛ませるようにします。
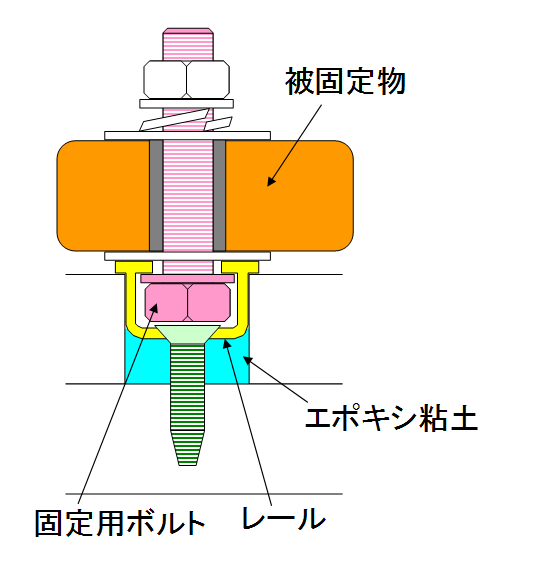
それでも負けてしまう場合には、再考することとします。