このページには、一部PDFファイルを利用しておりますので、閲覧にはAdobe readerなどの閲覧アプリが必要です。
製作記 関連
『作業台の製作概要および作業冶具案について』
2015.9.24
作業台の製作記概要と各種冶具のアイデアをPDFにまとめました。
pdfファイル:
PDFファイル 作業台製作概要と各種アイデア
『カメラグリップの製作概要』
2015.5.3
オリンパスOM-D EM5のカメラグリップ製作記概要をPDFにまとめました。
pdfファイル:
PDFファイル カメラグリップ概要
『AR-2 新フローターについて その2』
2018.1.22
ジンバル部分の再設計について、予定通り、重心を支点の下方に移す設計を行いました。
PDFに纏めましたので、そちらを参照願います。
pdfファイル:
『ジンバル再設計』
『AR-2 新フローターについて その1』
2018.1.20
Alpair−6Pの生産中止を知るのが遅れ、AR−2用のユニットが購入できなかったことがショックだったのは事実ですが、代わりに購入したAlpair−10Pをそのままの状態で約半年も放置してしまいました。
その間、環境の変化から製作が出来ない状態が続いており、それゆえ設計のほうにも力が入りませんでした。
購入したユニットに罪はありません。一念発起、重い腰を上げて、Alpair−10Pに対応した設計をスタートしました。
まず、フローターの設計です。
Alpair−6P用に低発砲塩ビで途中まで作ったものは、残念ながら再利用は難しいので、新規設計になります。
元々設計していた構造は、以下のようなものでした。
アキシャル、ラジアル方向ともに出来る限り位置を固定できるように設計しましたが、今回、「ラジアル方向の位置を決める必要があるのか?」を再考しました。
まず、フローター機能が正しく働くための要因を特性要因図で整理しました。
この図を元に、ラジアル方向の位置を決める必要性を考えてみます。
・スピーカーユニットは中心軸に対して軸対称なので、デザイン要素以外は必ずしも必要ではないが、内部配線の余裕がないと位置によっては突っ張り、そのストレスによる応力歪が問題になる可能性がある。⇒ ストレスフリーの配線方法は?
・構造をシンプルにするメリットが大きい。 ⇒ ネオジウム磁石の使用量を少なくできる ⇒ 漏洩磁界減少やコストダウンなどのメリットが大きい。⇒ AR構造は、前後方向に自己復元性の無い「やじろべぇ」構造(重心が支点より上にある)だが、支持シャフトの垂直さえ出ていれば反発力はさほど必要ない。⇒ そもそも重心を支点より下にすれば良いのでは? ⇒ エンジン保持部分の保持構造見直しが必要か・・・。
・エンジン部分でバランスが取れていれば、インシュレータは不要では? ⇒ だが、エアタイト構造(エア漏れ防止)は必要 ⇒ 無反発の漏洩防止は?
特性要因図の良いところは、「骨」を細かくしていく(因子を掘り下げていく)過程で、対応すべきポイントが浮き彫りになってくることです。
まず、ラジアル方向をフリーにした場合の構造を考えてみました。
図のピンク色の部分がインシュレータになります。まだ、排除していませんが、課題として残しておきます。
次は、やじろべぇの重心を変更する検討に入ります。
物事は、多角的に進めたほうが合理的です。(実は、飽きっぽいのですが・・・)
『作業台のフェンス案 その2』
2017.9.18
家にあった材料で具体的なスライダー案を作りました。
ベアリングは外径φ14、内径φ8で、アルミ丸棒φ8をカットして使うことにしました。
角フレームは□30と□15を使います。共に厚さは2mmですので、強度的には弱いため、別のパーツを組み合わせて強度を稼ぎます。
作業台に実装する部分は以下のようになります。
奥側は以下のように考えました。
今日は気圧の関係からか、急に気温が上がったからか、朝から頭痛がひどかったので、軽くなった午後から考えてみました。
『作業台のフェンス案』をアップしました。
2017.9.17
三連休は台風とバッティング・・・天気は最悪。
外は雨だけでなく、風も強くなってきました。
体調も芳しくないので、どうしてもアイデアくらいしか出せません。
今日は、作業台のフェンスについてです。
ウェブで探すと『手作りフェンス』は数あれど、高度な金属加工が必要で「おおがかり」だったり、強度不足で指で押すとグラグラしたりで真似をする気になれませんでした。
PINTERESTという画像のピンを多数得られるページに登録しているので、そこからベアリングのアイデアをいただいてしまいました。
Lアングルにベアリングの組合せでしたが、それをアレンジして角フレームとの組み合わせにしました。このほうが取り付け面が確保できるので利便性は高いと思います。以下にスライダ部分の構造を示します。
ベアリングでできる90度のアングルに別の角フレームを挟み込むことでリニアトラッキング構造を作ろうというものです。
手作りフェンスで気になっていたのは、どの案も片持ちで手前側はきちんと固定できますが、奥に行くほどブレて寸法精度が出ません。
両持ちで且つスムーズに動く方法は無いものかと考え、最初はスライドレールを考えましたが、1m以上のものは1セット1万円以上の高価なものになり、貧乏シロウトには手が出ません。
そこでアイデアを求めて上記のベアリングに辿り着きました。
既に作成した作業台に追加することになるのですが、実際の材料を想定して細かい寸法までは出していません。今回は、あくまでイメージまでです。
ベアリングが接する角フレームがトラックレールになるのですが、フェンスがベアリングのスライダに乗ることでベアリングがレールに押し付けられるような構造になります。
奥側のベアリング部分に寸法吸収構造を設けることで、スライドさせた時に動作抵抗が均一になるようにしました。
今回の案では、フェンス位置を決めた後に固定する構造は、単純な押しネジにしましたが、緩んだり、ズレたりしないような構造を探してみようと思っています。
今週は、ここまでです。来週は忙しく、再来週はインターナショナルオーディオショーのため作業は無理ですので、次の記事は10月に入ってからになります。
【追記】
固定ネジを締めた時のスライダーの浮き上がりが気になり、3方向からレールを挟むように変更しました。
動作の軽さはスポイルされるかもしれませんが、安定性は向上します。
『AR-1 ピアノ塗装 下準備編 その1』
2017.8.20
昨日に続き、AR-1の下地整形を実施しました。
まだ木工旋盤を紹介していませんでしたので、以下に掲載します。
大きなものを加工する旋盤にしては非力に見えると思います。もとより強度計算などせずに思いつきでデザインしたものをこの夏季休暇に作業に使おうと思い立って無謀にもそのまま作ってしまったので、危険なのは理解しているのですが、既に形状の出来ているものを追加工するのならば大丈夫だろうと思ってスタートしました。
思いの外、AR-1の形状は歪んでいたようです。目視しながらの手作業でしたので・・・言い訳です。塗装が残っている部分は凹んでいるために、まだ削れていないところです。
今日中には整形まで完成させようと頑張ったのですが、木製の固定冶具が壊れてしまい途中でリタイヤ。ありあわせの端材から切り出したので、木目に沿って割れてしまいました。やはり、きちんと強度を考えて作らないと怪我をしますね・・・。キャビネットの質量は3kg弱なのに回転させるとちょっとした偏芯でもモーメントが大きいので芯ブレがすごく、台座がゴトゴトと揺れるので、足で乗って体重をかけても収まりませんでした。中断後に確認したところ、芯出しをしなかったサブキャビネット側で3mmほど芯がずれていました。ほとんど外殻だけのようなキャビネットですから、これだけのズレでもかなりのモーメント偏りになっていたと思われます。たぶん、旋盤の強度を上げていたら、もっと早く冶具が壊れていたでしょう。ベースへの揺れ戻し(反作用)を抑えることになるので・・・。ここでも作用・反作用を実感してしまいました。
今週はここまでにします。
フローター部の製作 その1
- PDFファイル フローター製作記 その1
2016.5.8
円切抜き冶具の調整も 5/1 一杯で終わりましたが、5/2 に歯医者に行く事になりバタバタしていたので、フローター部分の製作作業は実質 5/3 からとなりました。
作業台を駐車スペースに持ち出し、ルーターにビットを取り付けてスイッチON。ルーターには悪いことをしましたが、1月に購入してから初めて稼動させます。
円切抜き冶具の一号機が小さな円を切り抜けず、二号機が完成するのを待ったのが原因ではありますが、花粉症で屋外作業ができなかった(・・・する気にならなかった)のが本音です。
ソフトスタートが効いている??若干、立ち上がりがスムーズ?かな〜と思う間もなくすぐに定常回転になる感じなので良く分かりません。
小型のソフトスタート無しのトリマーを一度だけ使ったことがありますが、確かに直ぐに立ち上がり定常回転だった記憶があります。1秒以下でも徐々に回転が上がることで反動が無いと理解すべきなのでしょう。
PDFの本文にも書きましたが、いきなり添付されていたφ12径のストレートビットを使う勇気が無く、別購入したベアリング付きφ6ストレートビットのベアリングを外してのトライとなりました。
軟質塩ビで、あまり高回転にすると熱で溶けてしまうのではないかと思い、回転数は20000rpm(目盛り5)としました。また粘りのある材料なので、切削時の負荷も気になるところです。
円切抜き冶具は、出来る限りバックラッシュを排除するようにしましたが、スライダとベースの間は約0.6mmの隙間(片側0.3mm程度)があり、スライダと直角方向に、0.3mm程度のガタが発生します。
このガタが、仕上がりにどの程度影響があるのか心配でした。
いきなり軟質塩ビにかかる訳にもいきませんので、手持ちのMDF(木質繊維板)でテストしてみました。
切り抜き冶具の抜き径設定にはコツが必要です。ビットの切削最大径になるのは刃が材料に一番近いところになりますが、これを見極めるのが難しい。トライ&エラーで決めるのも良いのですが・・・ルーターを裏返してMDF端材をベースに沿わせた状態にしておいてビットを手で回転させ、触るか触らないかの位置でMDFを固定して半径を計測。
トライ&エラーで詰めることにしました。
慣れればスケールを当てることで可能になるのでしょうが、まだ不安があります。
作業台の上に捨て材を置き、試験切り抜き用MDFの中心にφ8の穴を開けて冶具の中心シャフトを挿し込んでルーターを材料の上で回転させて切り抜いてみます。
まず気付くのが電源ケーブルが作業の邪魔になるということです。
次に材料を回してみますが、ルーターを片手で支えながら材料を回しているうちに、だんだん作業台の上を移動していきます。不安定なので、これも不可です。且つ、160mm以下の切り抜きにはシャフトがベース下に突き出るため、シャフトの逃げが必要になります。
そこで、作業台の端の部分に細工をして、シャフトを固定して逃げを持たせるようにしました。
実際に作業をしてみると、ビットが作業台の外に出るように保持するため、別の意味で難しいこともありますが、材料をCW(時計回り)に回転させつつ、ルーターをCCW(反時計回り)に移動させる作業を繰り返し行うので、ケーブルも邪魔にならず、作業位置も一定しているため、安定します。
以下は、撮影のためにルーターを作業台の上に置いていますが、作業はルーターのビットが作業台手前に食み出すような位置にして行います。
食み出すというとルーターの重量が原因で作業の際の重心が作業台から食み出て不安定のように感じますが、実際には切り抜く材料の上にルーターが載るかたちになりますので、極端に薄い材料でなければ問題ありません。(ビットを作業台端面に近い位置でしか動かさないようにすれば、被加工材料がたわんで作業に影響を与えることもありません)
この方法で切り抜いた材料を見ると、作業を繰り返す際に一度留めた部分に跡が残っています。加工中に力を加えていて力を抜いたタイミングですので、前述したガタの影響と思われます。
深さは0.1〜0.2mm程度ですが、指でなぞってみると凹みが分かります。冶具の改善点が見つかりました。
予定通り、50枚ほどの材料を切り抜き、一日目の作業を終えました。
二日目は位置決め穴と外周固定穴の加工ですが、円切り抜きの前にこれらの位置をポンチ打ちしておかなければならなかったことに気付きました。要は、中心が穴になってしまったので位置を出すための基準が無くなってしまったということです。
急がば回れで残っていた端材を探し出してガイド冶具を作り、ガイドに合わせてボール盤で穴加工をしました。
ここで、もう一つミスを犯しました。
位置決め穴は120°振り分けの3箇所になりますが、何を勘違いしたか、次工程の穴開け用に打っておいたポンチの部分までφ8の穴を開けてしまいました。(60°振り分けで6箇所)
翌日になり、気が付きましたが後の祭り・・・。4枚または8枚を重ねて穴を広げる作業となりましたが、ここでまたミス!φ10で穴を開ける作業で、油断をしたため材料をドリル刃に持っていかれました。
結果は惨憺たるもの。割れと欠け、偏芯と削り過ぎのオンパレード。
目も当てられませんでしたが、予備の材料は無し。
はて、どうしたものか・・・30分くらい途方に暮れていましたが、やってしまったものはどうしようもない。
ええい、ままよ!逃げ穴をφ12に広げて対処してしまいました。
これでどうにか使えそうです。
次の日は貼り合わせ。前後方向で非対称の貼り合わせとなる工程ですので、合わせマークが重要になります。
貼り合わせる前に位置決め穴が合っていることを確認してから貼り合わせていきますが、この時に前後の貼り合わせ位置を勘違いすると組めなくなります。(1セット間違えて、貼り直しました・・・つくずく注意力散漫な性格を呪います)
最終的に、28枚12セットを貼り終わりました。
ここまでで、タイムアップ!
最終日の5/8は休養日にしますので、続きは来週以降になります。
ここまでの途中経過を製作記にしました。
フローター加工手順の修正
- PDFファイル フローターの作成手順(改)
2016.3.12
花粉最盛期です!窓のサッシには黄色い花粉が溜まっていました。
今週も室内での作業になり、円切抜き冶具の製作を進めながら、フローターの材料手配と製作手順の見直しを行いました。
まず、低発泡塩ビシートですが、試作の回数が予想を超えたため、当初、余裕と思って12枚購入した特売品(450x600 t3 @470)が既に6枚となってしまいました。
このままでは材料不足となるため再購入が必要です。
WEBで探してみると、ブランド物しかありません。仕方なく、アクリサンデー フォーレックス(低発泡塩ビ板) 白 M(450×600) 5ミリ (E-7001 M 5)を2枚注文しました。
単価は2690円・・・想定した経費で作ることを狙っていますが『想定外の出費』ということで自分を納得させて発注。もちろん、板取り設計をして、最低限の2枚を発注しました。
注文した後になり以前の購入先が気になり確認したところ、@1520・・・失敗しました。まぁ、量産の時には、こちらから入手すれば良いということですね。マイナス思考は良いことがないので・・。
それはそうと、一部を5mmの塩ビ板にしたため、以下のように構造を単純化できました。
明日は試作品フローターから使える磁石を回収し、不足分を発注する予定です。
AR-2フローターNo.2製作記 中編その3
- 中編その3.pdf
2014.12.29
フローターの最後の課題になっていたラジアル方向の安定構造を検証しました。
詳細はPDFファイルを見ていただくとして、エントロピーの考え方が重要なことをまたまた実感。
『自然の事象(不可逆事象)はエントロピーが増加する(自由度が大きくなる=乱雑になる)方向に変化する』という基本的な考え方を間違えなければ、結果を類推することができます。
結果的には半分成功、半分失敗。
ラジアル方向については中心に保持することができましたが、スラスト方向への影響が出てしまいました (^_^;)
何はともあれ、影響への対処方法も思いつき、来年からは具体的な設計に入れる目処がつきました。
AR-2フローターNo.2製作記 中編その2
- フローター製作記・中編その2.pdf
磁石が入手できたため、ラジアル方向の安定浮遊に関する基礎実験を行いました。
私の勘違いから買わなくても良い磁石まで購入してしまいましたが、メゲずに実験してみました。
4回目の報告になります。
結果、ラジアル方向(ユニットを中心に保持する方向)の安定浮遊の見込みがつきました。
5回目については、何とか今年中には報告したいと考えています。
AR-2フローターNo.2製作記 中編
- フローター製作記・中編.pdf
夏休み以降、連休が何回かありましたが、休日出勤が重なったりで色々忙しく、半日単位の作業が続きました。
それでもコツコツ作業した甲斐があり、やっとスラスト方向(ユニットに対して前後方向)の検証が出来ました。
3回目の報告になります。
次は、ラジアル方向(ユニットを中心に保持する方向)の安定浮遊に挑みます。
今年中には報告したいと考えています。
試作機AR-1の改造について
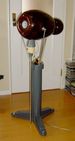
流線型の合板積層キャビネット部と一脚ピラーが特徴の試作機AR-1に改造を実施しました。
実験経過に基づいた改善です。
対になる後方ユニットからの放射音圧が後方に減衰せずに放射されることで歪みが発生していたことへの対策になります。
写真を中心に紹介しています。
AR-1の試作に使用した工具/冶具について
試作作業に使用した工具や冶具、製作のノウハウを紹介します。
1.大型円定規
径の違うリング状の板材を何枚も切り出すため、自家製の円定規を作成しました。
市販のSUS製スケールを利用したもので、基準端(0mm)の部分にボールペンの先端が入る溝を端部中央に設けてあり、墨入れ(円を描く作業)の際にはボールペン先端を溝に嵌めます。
ネジの先端を尖らせた中心固定部分を指で押さえながら円を描くという簡単な構造ですが、板取りの際には、重宝しました。
市販品が見当たらなかったので作りました。お持ちのスケールに合わせて製作されると良いと思います。
2.自由錐(サークルカッター)
神沢鉄工所という会社のK-102『厚板用』というものを使いました。
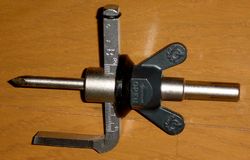
電動ドリルにチャックして使います。
穴あけ範囲はφ40〜φ120で、今回は、支柱部分を外形φ100内径φ45のドーナツ状の板を12mm厚の針葉樹合板から切り出したので、内径の切り抜きには重宝しました。
連続して使うと熱を持つので、4個くらい抜いたら、錐が冷めるのを待つ間にジグソーで外形抜きをするというような作業としました。
片側の支柱だけでも42枚必要でしたので、最後にはチップ刃が鈍ってしまいました・・。
3.ダクト製作用にプリンの容器を流用しました
円錐台形状のダクトを製作するのに適当な型としてプリンの空容器を使いました。
表面を塗装で仕上げる構想でしたので、新聞の折込み広告を型の上に貼り重ねてダクトを作る方法を採りました。
強度を得るために木工ボンドを水で薄めたものを一層毎に塗り、貼り重ねる方法です。
実際には、約5mmを貼り重ね、半乾きの状態で一日放置し、翌日、更に3mmくらいを貼り重ねる作業になりました。
作業を短時間で上げたかったために2回の工程にしたのですが、これがアダになりました。
一度に厚く貼り重ねたため、乾燥するに従いシワが発生してしまいました。
おまけに内部の水分がなかなか抜けず、却って乾燥時間が長くなりました。(夏場でも約1週間!)
(詳細は『製作記』をご覧ください)
AR-1のサイレンサー構造追加改造の製作記
本体キャビネットの後方にサイレンサー構造を追加する事で、気になっていた後方からの音漏れによる混変調歪を減らすことが目的です。
スチフネスの改善を考えると容量を大きくしたほうが良いのですが、バランス上、サイレンサーの大きさには制限があります。
AR-2への試金石として製作に踏み切りました。
AR-1の製作
木取りから接着〜組み立て〜塗装までを写真と文章で紹介
(PDFファイルを利用していますので、Abobe reader などの閲覧アプリが必要です)
・ドライバユニットAlpair-6PをARシステムに対応させるための改造
・ボディの加工〜塗装
・スタンド(支柱)部分の塗装について
・ダクトの製作〜アンカーシャフトの防振加工
などを紹介しています。
設計寸法について
AR-1の設計寸法と板取寸法図面です。
製作工具/冶具について
試作機AR-1の製作にあたり使用した工具や冶具を紹介しました。