立坑櫓 その構造と制御
《目次》
- 温存された斜坑群
- A型櫓 4本索の夢
- オールケージ
- 自動化への道
- 自動デッキチェンジ
- 湧出量300立米/minのCH4
※目次クリックからリンクしています
立坑を中心とした地質構造の断面図である。
赤平炭鉱は北海道中央部に位置し、国道38号線とJR根室本線に隣接、交通至便な立地環境だ。
赤平駅の東南960mに選炭工場を有し、これに接して第一立坑、その他諸設備が集約されている。
褶曲地層
石炭を採掘する場合、地表表面層に「炭層」石炭の含まれている地層
が露出していれば、
それは露天掘りという工法で、表土を剥土して容易に採炭可能だ。
ところが一般に石炭は地中深くに存在し、しかも炭層は厚く水平に広がらず、
断層で切断されたり、地圧で波のように褶曲して存在している。
また炭層内はすべて均一に石炭の層だけでできているわけでなく、
間に石炭以外の岩石や砂が混在しているのが一般的だ。
それらを含んだ炭層全体の高さを『山丈』、石炭の部分だけを集約して合算した部分を『炭丈』と呼ぶ。
つまり、『炭丈』が大きいほどその割合が多く、条件が良いこととなる。
実際、赤平においても上図のように東西の鉱区境が高く、中央の第一立坑付近が『Uの字』に最も陥没している。
地表から浅い部分は機械化が進まず、深部につれて傾斜が緩くなり機械化が可能となってくる。
立坑建設以前、炭層が傾斜をもって地中深くに続く赤平のような場合には、
その炭層に沿って掘進することで炭層の採炭現場に至る斜めの坑道、つまり斜坑が出来上がることとなる。
立坑完成前 坑道配置 ( fig.1)
前述のとおり稼行に耐える0.6m以上の炭層は23枚で、この平均山丈2.15m、範囲約18平方キロの鉱区内にある炭量は、
-1,200mまで推定され、算出された推定炭量はおよそ4憶t。
ところが昭和14年以来、20年以上稼行してきたことにより、-350L水平上部の炭量が減少してきたのは事実であった。
石炭政策
この頃の時代背景として、政府は石炭鉱業合理化臨時措置法の策定に至り、
貯炭増による出炭制限や過剰人員の削減、非能率な老朽化炭鉱の廃止などと共に、
業界全体が若返り、そして技術革新と大規模な合理化、体質改善の形而下を打ち出す時期にあった。
そこで、拡大生産を目指すビルド坑である赤平炭鉱は、新区画の開発の必要性を検証し、
立坑開削による深部開発を契機として、坑内外の幅広い合理化を図り生産規模を拡大することを一連とした、
設備投資計画を立案することと相成った。
立坑完成後 坑道配置 ( fig.2)
つまり、-350L以下への展開、そこから垂直200m間の-550Lまでを『深部』と呼び、
深部開発委員会による経済的実収の検討がなされた。
-350Lから-550Lまでの深部には予測炭量が3,700万t存在し、将来の採掘量200万t/年としても、
20年近い寿命があると積算し、この-550Lを最初の深部の『底』と取り決めたのである。
-550L坑底
( fig.1)にある通り、従来斜坑のみの場合は
「コース巻き」コース(綱首)を炭車(トロッコ)に連結し斜坑上部の巻上機で運転する斜坑運搬方法
が6本
「スキップ」石炭/ズリを運搬する専用箱
が1本であった。
三交代制操業でコース巻きは80万t/年、スキップは64万t/年の合計144万t/年となり、
この数多い巻上機の集約こそが坑内外の合理化にも繋がると検討された。
ズリの坑道充填
立坑巻上能力は140万t/年であるから揚炭を集約するために、その能力を補う必要があった。
この立坑巻能力不足の要因、これは赤平坑特有の急傾斜坑にあった。
つまり、年間目標予定200万tの採掘に見合う、
「水洗ズリ」原炭から必要な石炭を抽出した後の屑
の坑道充填が必要だったのである。
他炭鉱に比較して自然発火しやすい特質にあった本坑は、その防止のため、
再び立坑の下り便を利用してズリを搬入、坑道に充填したのである。
そのため、立坑は揚炭だけでなくズリの下降にも利用され、これが能力不足の一要因となったのである。
坑口操車場
これを補うため、かつての1坑スキップ式斜坑は存続し併用されたのである。
元来、総コンクリートライニングの半永久坑道であった本坑は、
スキップをベルトコンベヤーに切替え、昭和38年9月、立坑完成から遅れること半年で操業開始した。
運搬量は500t/h、機長1,590m、傾斜度16°、ベルト幅1,050o、
ベルト速度150m/min、電動機350kw×3台という最新鋭のものであった。
ベルト斜坑(別炭鉱参考資料)
長尺部材の搬入
当坑の平均山丈は2.15mと厚層が多い。また断層も多く資材は長材が必然的に多くなる。
前述のとおり、立坑の降下時もケージには充填用ズリを積載した炭車で満車となる。
掘進は120m/日とすると、必要部材は10mレール24本/日、5mパイプ20本/日、鉄枠60枚/日となり、
立坑で運搬するとしても、ケージの屋根を取り外すか、
ケージの下部、テールロープに結び付けて卸すこととなる。
坑底そして各
「盲立坑」坑口が地上に出ない地底の立坑
でも同様の作業を繰り返す必要があり、
これらを合算すれば積込時間だけで16h/日を要し、これは非常に非効率だ。
材料斜坑(別炭鉱参考資料)
そこで検討されたのが、既存斜坑による長材の運搬である。
たまたま一坑本卸(fig.2)は非常に維持の容易な斜坑であり、
枠内段面13平米の広い鉄枠斜坑で、傾斜16°、延長1,700m、湧水が無く長年安定していた。
そこで、本坑を利用して長材を搬入することとなった。
このことは必然的に盲立坑を排して盲斜坑の建設要求となった。
結果、坑口で積載した長材は運搬車に積んだまま坑底に下る。
そしてそのまま盲斜坑を通って
「切羽」採掘現場の最先端に至ることとなる。
斜坑/立坑併用時の問題
立坑と斜坑を併用する場合、一番問題となるのが炭車(トロッコ)である。
突き詰めれば炭車(トロッコ)の連結装置である。
これまで炭車は斜坑専用機/立坑専用機であった。相違点は以下となる。
炭車相違点
斜坑を登坂する炭車なので接続部であるリンクはそれだけ強度が高い大型のものが必要がある。
対して立坑用は頻繁に連結・切り離しを行うので、軽量で容易なものでなくてはならない。
また斜坑用は片側ピン/反対側リンクのいわゆる『雄雌』があるため、
『逆ドロ』と言われる、雄同士/雌同士の向きにならないようスイッチバック等で注意が払われていたが、
対して立坑用は坑底でループ坑道を循環させるから、雄雌があってはならない。
坑底ループ坑道
この相反する両者の要求を満たす連結装置の検討に2年近くをかけ、
雄雌がありながらどちらでも共用でき、立坑積載時の段差による突き上げや、
斜坑登坂時の強度も兼ね備えた、新形状の連結器の完成に至ったのである。
新型連結器
@連結器本体A差しピンB補助ピンC操作ハンドルDスタットリンク
連結を切った状態では操作ハンドルCを倒すとスタットリンクDは連結器本体内部に格納状態となる。(雌状態)
連結する相手装置に接近させてから操作ハンドルCによりスタットリンクDを相手側の連結器本体@に差し込み(雄状態)
相手側差しピンAを差し込めば連結は完了する。
スタットリンクDを格納した状態のまま保持するために、補助ピンBで固定する。
つまりどちらもが雄になり雌になる雄雌兼用型連結器ということになる。
これで転回できない坑底でのループ循環にも対応した上で、強度的にも申し分ない炭車が完成したこととなる。
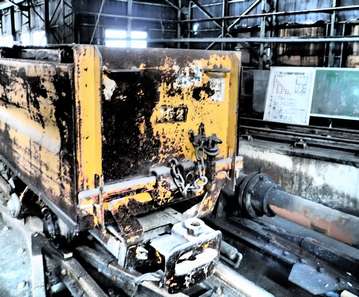
新型連結器
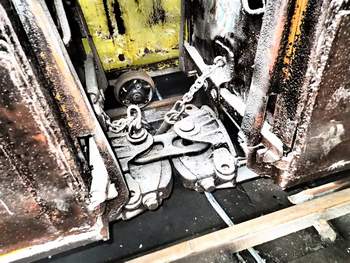
旧型連結器
他炭鉱では、立坑完成によって閉鎖される斜坑が多い中、
ズリ充填という立坑のロスを補填するために温存された斜坑併用操業、その兼用炭車の開発が特筆すべき注目点だ。
立坑櫓を形式的に分類すると、まず大きく二種類に大分される。
言わばメインの機器である
「ケーペプーリ」動力滑車
や電動機(=モーター)などが下部(地上付近)に設置される『グランドマシン』型。
一方、それら重量物が塔上に設置される『タワーマシン』型。
そしてそのグランドマシン型の中に、形状により『R』『A』『H』型などがある。
櫓形状の決定
赤平第一立坑はH型櫓を採用している。
H型に比較して約3%のコスト削減の計れるA型であるが、
その構造上、ワイヤーロープの坑外部分の振れが激しくなり、
互いに干渉し不具合の原因となること、そして建設の容易性からH型が採用されたようだ。
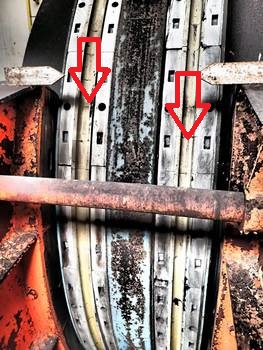
A羽幌運搬立坑
立坑のメインロープは直径50oの複数(2本)による運転方式、つまり多索式となる。
計画時は4本ロープ式という更に多綱式での検討がなされていた。
これは、ロープ直径が小径化できること、複数本による安全率の向上、
二次的効果としてのロープスリップの減少などが長所としてあげられるためである。
しかしながらロープ本数が増加すれば、一本ごとの伸び率不均衡により、
やがてそれぞれの長さに大きなばらつきが生じる。
また4本索以上の多索巻上機の場合には、構造上、「ヘッドシーブ」塔上の無動力滑車
の数量を増加させる必要があり、
ロープが電線のように櫓を走ることとなる。
これを避けるためには、巻上用の電動機(モータ)やケーペプーリなど重量物を塔上に配置する、
タワーマシン型の構造が必要となり、これは地震大国である日本では嫌う部分でもあった。
現地@赤平立坑のケーペプーリーにはワイヤーロープが這う4本の溝=
「ロープライニング」滑り止め
がある。
2本策式に対して4本の溝は不思議な感じがするが、恐らく奔別同様に摩耗に備えての予備溝であり、
同一ライニングを長期的に使用するための策だと思われる。
A羽幌運搬立坑に至っては2本策式の2本溝となっている。
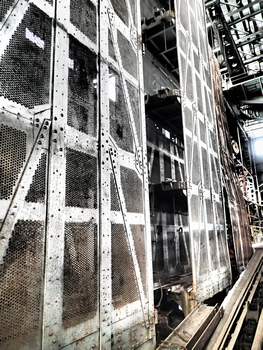
赤平立坑ケージ( fig.3)
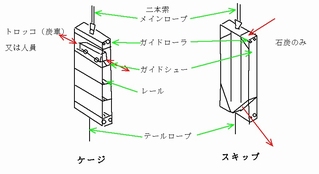
ケージ/スキップ模式図( fig.4)
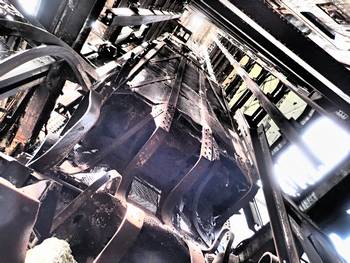
奔別立坑スキップ( fig.5)
立坑における運搬装置
立坑の目的は、短時間で採炭現場に人や資材を運搬し、原炭を地上へ搬出することである。
地中深くの炭層に人や物を運ぶエレベーターにあたるため、その運搬装置は大きく二種ある。( fig.4)
・ケージ( fig.3)
人員または石炭を積んだトロッコ(炭車)を載せる1〜4階建ての箱
内部にはレールが敷設、トロッコ(炭車)に石炭を積んだままケージに乗り降りさせる
(赤平仕様)4段デッキ 定員72名=4.18t/一段18名 炭車×4台=8t、ズリ車×4台=12t
(短所)ケージ床面とデッキ軌道面は段差なく緩やかにトロッコ(炭車)を載せるため、要求着床誤差は±18o
・スキップ( fig.5)
石炭専用の運搬用箱
坑底に積込シュートを設置、スキップ上部の開口部へ原炭を流し込む。
地上坑口では排出ホッパにスキップ下部の開口部から原炭を排出する。
(短所)その際、落下落差の関係で石炭の粉化(粉砕)が発生する。
ケージ/ケージとされた理由
ケージに石炭積載トロッコが満車の場合と、スキップに石炭を規定量までバラ積みした場合、
重量的にはケージの方が若干軽量となるが、その重量差は誤差の範囲程度となり問題とはならない。
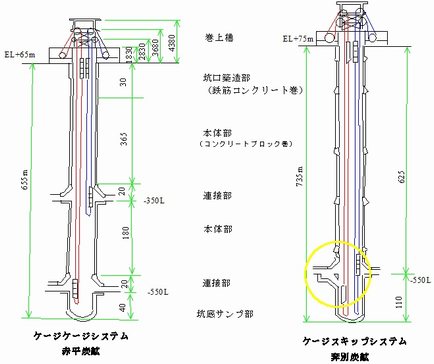
ケージ/スキップ比較図( fig.6)
左側が左右両ケージ仕様の赤平第一立坑、右側が左スキップ/右ケージの奔別立坑である。(fig.6)
黄色丸部に注目していただきたい。(fig.6右)
・坑外よりのズリ搬入
スキップは基本、坑底で石炭を積込み、地上で排出する。
そのため坑底に一連の積込施設であるメジャリングポケットやスライドゲート、
積込シュートなどを設備し、停止位置もスキップ上端が坑底シュート下端となる。
つまり、坑底で地上から降ろした充填用のズリを排出することは想定されていないのである。
前述のとおり、赤平炭鉱は急傾斜坑であり、採掘した坑道維持のため、
多量の充填用のズリを坑底に運搬する必要があり、これにはスキップは不向きと考えられたのである。
・炭種別揚炭
赤平炭鉱では70%以上の(高級)原料炭と30%の一般炭を産出していた。
原料炭の商品炭は6.5%の低灰分を保証品位として要求されるから、
原料炭/一般原料炭そして更に低灰分の高級品と三色選炭も視野に入れていた。
スキップによって炭種別揚炭を施工する場合、坑底に複数の類別ポケットを設備しておく必要があり、
炭種ごとに時間別揚炭の作業が伴い、これは非常に煩雑化を招く。
より複雑なスキップ坑底設備を要求し、炭車操作も含めて実用的でなかったため、
スキップの不採用となったのである。
・人員昇降の迅速化
ケージ/スキップ併用の場合は片側にしか人員が乗降できないため、
入昇坑時間のロスが大きい。
-350Lの坑底まで斜坑人車では片道10分を要していたものが、立坑では1分足らずで到着するのである。
以上三点の理由により、赤平第一立坑ではケージ/ケージのオールケージシステムが採用されたのである。
立坑巻上機は一般機械とかなり異なった性質を持っている。
地上で定位置に停止したケージに人員またはズリを積んだ炭車が積載される。
坑底では原炭を積込んだ炭車が数台載せられる。
なだらかに降下、加速しスタートから14.5秒で最高速の12m/secに到達。
その最高速は23.3秒続き、残り50m、9.7秒間で減速し微速から4.1秒で規定の位置に停止する。
その間550mを合計わずか51.6秒。
昭和38年完成姿
これは運転者がレバーによる手動運転を行い、
ロッドや歯車を介して機械的接触による作動や制動を行っても時間的に間に合わない。
巻上工程の毎回1秒のロスは年間1〜2%の出炭減になると言われる。
これは具体的な物量でいえば、4t/年である。実際、それほどシビアな制御なのである。
そのため目指したのは1ボタンによる1サイクル自動運転、そして精密着床の1
「デッキチェンジ」炭車の段階的積み替え作業
自動運転である。
これは運転のスピードアップ、容量の増大化、事故の皆無、容易な運転を求めた結果である。
マウスon
ワードレオナード制御
立坑は正にエレベーターであり、その運転速度は刻々と変化する。
停止から加速、最高速から減速、再停止とケージを操るケーペプーリの回転数は
0〜41.7rpmまで制御の必要がある。
ケーペプーリを駆動する電動機(モーター)は直流(DC)方式と交流(AC)方式がある。
従来大型立坑巻上機は
「直流(DC)方式」(DC=direct current)流れる方向と電圧が一定の電流
が主流であった。
「交流(AC)方式」(AC=alternating current)流れる方向と電圧が周期的に変化する電流
は小型巻上機に限られていたが、
奔別立坑ケージ側には減速装置の進化に伴い
1540Kw交流(AC)方式が採用されたものの、まだまだ直流(DC)方式が主流の時代であった。
直流(DC)方式が交流(AC)方式に勝る点は任意の中間速度でエネルギーの損失が無く、
余剰エネルギーを電源に戻すことで制動力が得られ、負荷の影響を受けにくいことである。
そして何よりそのトルク(力)の大きさと回転数制御の簡易性が大きい。
交流(AC)方式はこれに対して起動時のエネルギー損失が過大で、
同期速度以下では制動力を発生せず、負荷の影響も受けやすいものの、コストは抑えられる。
そして「インバータ」半導体で電源周波数を変化させて回転数制御を行う
の無い時代、回転数の制御が困難な点が大きい。
赤平立坑に至っても直流(DC)方式の採用に至り、
その回転数制御はワードレオナードという方式を採用した。
これは外部商用電源(200V 3相)を用いて1800Kw交流(AC)同期電動機(モーター)を定格駆動し、
これにシャフトで直結した1800Kw直流(DC)主発電機を稼動させ、発生した直流(DC)電源を、
「界磁制御」モーターが作る磁界の磁束密度を調整することで回転数制御を行う
することでその電流値を変化させ、その制御可能となった電源を用いて
ケーペプーリに直結した、1600Kw直流(DC)電動機の回転数コントロールを行うものである。
複雑なようだが現代なら
「AC/DCコンバータ」大電流の交流を整流して直流化、可変電圧にて回転数制御を行う
や
インバータ
を用いて
簡素に電動機の回転数コントロールが可能であるが、当時はまだその技術が無かったのである。
巻上機の作動
機構配置図
基本動作としては、以下となる。
a,外部商用3相200V電源で@AC電動機を定格運転
b,@に接続したADC発電機を駆動
c,B励磁用電動機・発電機で、駆動したADC発電機の電流や回転方向を制御
d,その変化させたDC電流でC駆動用DC電動機を運転(回転数コントロールを行う)
e,C駆動用DC電動機に接続したDケーペプーリが回転、巻上げ,巻降ろしを行う
f,Dケーペプーリの回転数がE運転調整器に伝達
g,ケージ位置を演算、確認しながらプログラムの信号により加速、減速を行う
h,必要な場所でエア式シリンダー(赤)を作動させてF常用ブレーキを上部へ作動
i,Dケーペプーリを両側から挟み込むようにブレーキ作動
j,停止時、非常時はG非常用ブレーキのエア式シリンダー(赤)を作動させて重石を下部方向に作動させる
k,Dケーペプーリを両側から挟み込むようにブレーキ作動、同時に流れる電流も減少させる。
この特異な運転特徴を自動化するには、制御装置として以下の点において十分考慮されたものでなくてはならない。
1、最大の出炭量をあげるため、加速度及び微速度を増大し、能率的なプログラム運転を行う。
2、精密着床、デッキチェンジのための必要な低速度が確実に得られること。
(0.3m/sec程度で全速の1/60〜1/70)
また、巻上機に連動するパルス発生器からの積算によりケージ位置を検出し減速開始、停止等の指令を行うこと。
3、加速及び減速電流の最高値が許容範囲内であること。
4、巻上機に連動する運転調整器及び無接点
「継電器」回路内の電流を遮断したり方向を変えて、他の回路スイッチの開閉を自動的に行う装置
により、時々刻々とケージ位置を検出、
プログラムに従った速度指令を行うこと。
5、非常制動に際しては機械的なメカブレーキだけでなく、
電源の「励磁」コイルに電流を流して磁界を作ること
を急速に消勢させたうえで非常用制動機を作動させること。
つまり自動化の要は現状のケージ位置を把握して、
その後の動作を指令する『運転調整器』と『無接点継電器』の働きによる部分が大きい。
運転調整器
プログラム指令の骨子は巻上機の回転に直結した運転調整器である。
運転調整器
今回現物の確認は行えなかったが、上記写真が完成時の運転調整器である。
これは運転台の地下にあり、巻上機制御の中枢をなすものである。
ケーペプーリに連動するロッドと直結し、プーリの回転に従ってカムを持つ制御円盤が回転し、
その縮尺率1/400の回転からパルスが発信され、深度に応じた速度指令が出される。
ただ、ロープの伸びとスリップがイレギュラーの要素として発生するため、
1サイクル作動完了ごとにケージのゼロ位置停止時、
ストップモータにより制御円盤の回転位置の原点復帰を行い、
ロープの伸び、
「クリープ現象」持続応力により時間経過とともに歪方向に動作する現象
、ロープスリップなどを校正しその影響を機械的に除いた。
無接点継電器
また、本来はこの運転調整器で自動運転のプログラム速度指令を行うが、
実際のケージ動作状態を検出するため、多数の制限開閉器を設置しその信頼性が高められた。
以前の制限開閉器はレバーやピンを用い、メカ的な接触により機械の位置検出を行っていた。
立坑内は常時保守の行き届かない個所も多く、
誤動作、可動部分の摩耗、電気接点の不良などが発生しやすく、
消耗に対しての信頼性が著しく低かった。
そこで新たに開発されたのが『ノンタクトリミットスイッチ』無接点
継電器
(NLS)である。
ノンタクトリミットスイッチ
これは検出器と作動子(永久磁石)からなり、検出器は鉄心とコイルの単純構造である。
検出器付近をケージに設置された永久磁石が接近通過することで動作し、機械的な接触無しに信号を発信する。
押しボタンや操作部が存在せず、無接点化は秒速12mという高速に対応した。
このNLSは坑口より100m下に、ロープスリップ監視用として装着、
その他、ケージ停止位置、そして強制微速指令用のNLSが停止位置の1m手前に装着されていた。
これらNLSからの信号はいくつかの回路を経由して、自動運転用エア回路の電磁弁を消勢させ、
常用制動をかけるのである。
制動に関わる回路については即応性が必要で、新回路はNLS動作後0.3秒で制動が掛かり、
これは当時としては最先端の技術であった。
その結果、±12tの過負荷テストケージにおいても±100oの着床精度を発揮し、
常用制動の機械的立ち上がり0.2〜0.25秒を含んでの0.3秒であるから、
これは相当な迅速性であると言える。
以上、ワードレオナードによる直流DC電動機の回転数制御と複数の機構によるケージ位置把握、
そこからのプログラム指令による制動機作動と、当時としてはまだ確立されていなかった
対象物の状態が目標値であるかをセンサで確認しながら、
一連の手順に従って工程を進めていく現代のシーケンスの考えにほど近い訳である。
ケージ内部
ケージ内部にはレールが敷設されている。
状況に応じてここには18名の人員か若しくは炭車(トロッコ)が積載されることとなる。
地上、または坑底の『デッキ』と呼ばれるプラットフォームから炭車をこのケージ内に搬入搬出する作業、
これが『デッキチェンジ』と呼ばれる作業だ。
ケージは4階建てのため本来は4回、ケージの停止位置を変更して、
積込積卸を行うわけだが、赤平では最終的に下図のように『上部デッキ』『下部デッキ』を建設し、
2回のデッキチェンジで炭車の搬入搬出が可能となっている。
ケージ積込模式図
トロッコ積載方法(デッキチェンジ)
@ケージ(赤枠)が上部デッキ/下部デッキと合う位置で停止
1段目/3段目にトロッコを載せる(降ろす)
Aケージが下部へ一段ずれて再停止
2段目/4段目にトロッコを載せる(降ろす)
しかしながらこのデッキチェンジに対しての要求は厳しい。
ケージ重量は満車で12t〜人員なら4.18tとその重量変化も大きく、
その中で作業は迅速に行え、デッキとケージ床面の着床精度は炭車が容易に押し出される程度、
つまり荷重の変化が大きい中、全行程550m中で±20o以内が要求される。
また停止時はロープの振動が少ないように緩やかに制動する必要があるし、
このデッキチェンジの能率がケージ巻上機の運搬能力を左右すると言っても過言ではない。
赤平立坑においてはこのデッキチェンジの自動化に労力が注がれた。
そのため、ケージ位置に従った速度と制動の自動プログラム制御が不可欠となる。
手動運転では1デッキチェンジ所要時間が4.3〜5.75秒であり、
このうち平均1秒が作業者の反応時間となっている。
自動化することで所要時間が3.4〜3.9秒に短縮され、停止時のロープ振動も軽減されることとなった。
自動デッキチェンジ盤
デッキチェンジのための制御
このため、ケージ位置の検出は必須項目となり、例えば運転調整器の縮尺率は1/400となっていて、
実際の1デッキチェンジ行程2mは運転調整器カムディスク上では5oであり、
その信号検出は非常にシビアなものとなる。
そして前述のロープスリップ、ロープの伸びにも対応するべく、新たに設置されたのがNLSであり、
デッキチェンジに関わる減速開始・停止の指令を出す位置を決定し、
発信されるパルスから計数的に位置検出を行った。
このように1パルス0.5pの通し算から積算した計数制御を採用した動機は、
恐らくロープスリップなどの要素から、後に調整可能な容易さを重視したのだと思われる。
プログラム回路とは別に、指令の検出とその実行内容の監視も行われ、
「サイリスタ」シリコン制御整流子 ある信号で
スイッチとなりonになり続けたり、双方向の電流を制御できる半導体素子
を用いた演算時に使用する
「関数」普通2進法+2進化10進法
を2種使用し、お互いに独立演算することで、
信頼性の倍増を図り、
「ロジット」演算時に利用する関数
「SCR」サイリスタ=シリコン制御整流子 ある信号で
スイッチとなりonになり続けたり、双方向の電流を制御できる半導体素子
制御を用いたトランジパック(通過)方式の確立に至ったのである。
赤平炭鉱が褶曲地層上に位置していることは前述したが、
この褶曲部のオメガカーブ内に堆積しやすいのが
メタンガス(CH4)
である。
無毒爆発性のメタンガス(CH4)は一般に数気圧、10〜30気圧の圧力を持っている。
無色、無味、無臭で比重は空気の1/2、つまり坑道では常にその上部に溜まり、
直接毒性は無いものの、空気中に40〜50%混合すると酸素濃度が著しく減少し、酸欠の危険性がある。
また、それ以上に恐ろしいのは空気中に5〜15%混入した場合の爆発性である。
保安の意味からも坑内に湧出するメタンガスを外部に排気するのは、
重要な通気の目的であり、その量が多い場合は専用に配管などを用いて抽出する必要がある。
発電2号機
ガスタービン発電施設
本坑では坑内ガスの有効利用として吸引したメタンガスによる7,000Kwのガスタービン発電施設を、
昭和39年(1964)に1号機、昭和40年(1965)に2号機と運転を開始し使用電力の60%を供給、
保安・操業電力、
また廃熱ボイラによる暖房用蒸気・浴場用温水設備として、
安価な電力・熱供給を行いコスト削減に寄与してきた。
しかしながら、昭和42(1967)〜46年(1971)をピークとしてガス抜き量は次第に減少し、
昭和54年には写真の2号機を運転停止、利用率も40%台に低下し、
その後昭和61年(1986)には約20%にまで低下するに至った。
そこで昭和62年(1987)には電力コスト削減対策として、発電設備の灯油燃焼化改造を実施することとなった。
そのため、屋外貯蔵タンクとその送給ポンプの設置、制御装置と監視制御盤の設置を追加した。
既存の制御回路は据え置きとし、灯油燃料の制御系を追加する形をとり、
既設バーナーも改造し混焼バーナーとすることで改造費の削減を行った。
本来、酸欠や爆発を誘発する余剰物質を再利用して、有効活用したその経済効果は大きい。
更に現状の設備を確認することで、東洋一と称された所以に迫りたいと思う。
立坑櫓メインへ
赤平第一立坑へ戻る