立坑櫓、その構造と制御
《目次》
- 立坑の構造
- 立坑櫓の分類
- 共同企業体
- 多索式の利点と短所
- 立坑開墾
- 巻上機制御方式
- スキップとケージ
- 自動運転化への道
※目次からリンクしています
立坑櫓の各部名称である。
下部の円が電動機(モーター)に接続した駆動用の
「ケーペプーリ」動力滑車。
上部の円4か所が
「ヘッドシーブ」無動力滑車
でワイヤーのスリップ防止のために、
シーブに巻き付くように急角度でワイヤーが接地している。
右側(青ライン)が「スキップ」地下で採掘した石炭を積込む箱で
左側(赤ライン)が「ケージ」人員・炭車輸送用の箱を
それぞれロープ末端に吊り下げて、坑底と地上を行き来する。
つまり、立坑坑道内に2種4個の箱が上下動していたこととなる。
ケーペプーリ
ケージは中にトロッコ用のレイルが敷設された、長方形の箱で
奔別では4階建てのケージが使用されていた。
高さは10mに及び、1段あたり人員16名(合計最大64名)、または2立米炭車1台(最大3車)、
を積載可能とし、巻上速度は最大12m/sec(時速約47q/h)というものだった。
つまり4階建ての箱のうち3箱には、人またはトロッコのどちらかが
その時の状況に合わせて乗ることができたことになる。
そしてこれは通常の人員エレベーターの10倍の速度にあたり、
現在でいう東京スカイツリー展望デッキエレベーターより高速であった。
ケージ
ケージ内部
4階建てのケージのうち3段にズリや原炭を積載したトロッコを積込むことが可能だったものの、
しかし地上に到達しても3台のトロッコを一度に降ろすことはできず、
ケージをずらして1台ずつ降ろすこととなり、この作業はデッキチェンジと呼ばれた。
一方、スキップは石炭・ズリ専用の輸送用搬器である。専用機ならではの多機能さは欠如するが、
前述のデッキチェンジの必要がなく、人員は乗降しないので、
更なる高速運転が許可されていた。
しかしながら、石炭の積込、搬出用の大掛かりな装置が必要となり、
その際、石炭の
「粉化」石炭が粉砕して粉状の炭塵が発生する
が起こり、これは選炭時のコストアップや環境への不具合をもたらした。
スキップ
立坑櫓を形式的に分類すると、まず大きく二種類に大分される。
言わばメインの機器である
「ケーペプーリ」動力滑車
や電動機(=モーター)などが下部(地上付近)に設置される『グランドマシン』型。
一方、それら重量物が塔上に設置される『タワーマシン』型。
そしてそのグランドマシン型の中に、形状により『R』『A』『H』型などがある。
鋼が引張・圧縮に対して強度が高く、軽量化が図れることから、
鋼製櫓が日本では主流となってきた。
地震の少ないドイツでは、台風も少なく高層建造物にとって立地がよく、
タワーマシン型の塔型櫓のシェアも大きい。
地震大国日本では、タワーマシン自体が非常に稀だ。
コスト比較を行った場合、塔型櫓はH型の+20%、A型は逆にー3%となっている。
R型はH型のー20%、A型に対してー17%となっている。
建設の容易性、美観そして、
「ガイドシーブ」ヘッドシーブ=無動力滑車への
ワイヤーの接地圧
からもH型に抜き出た高性能があるのは明白である。
マウスon
各構造物の担当メーカーと(技術提供企業)
奔別立坑建設の前段階で、将来の深度増加をも想定した計画の中で、
設備の発注に伴う主な仕様は以下であった。(詳細は別途解説)
スキップ巻上装置
DC直結式ワードレオナード制御方式
「ケーペ式」ドラムにロープを巻き取らず、
ヤジロベーのようにロープ両端で交互に地上と坑底を結ぶ
2本ロープ仕様
スキップ容量 10t 速度 秒速12m
運搬能力 400t/時
ケージ巻上装置
ACギヤ減速式 低周波制御方式
ケーペ式 2本ロープ仕様
ケージは4段 炭車3車
人員は64名 速度 秒速12m
長期工事計画
工期 |
深度(m) |
巻上距離(m) |
速度(m/s) |
第1期(前期) |
680 |
638 |
12(時速47km/h) |
第2期(前期) |
840 |
868 |
12(時速47km/h) |
第3期(後期) |
1050 |
1079 |
16(時速60km/h) |
第4期(後期) |
1260 |
1289 |
16(時速60km/h) |
これら設備について、メーカー提出仕様書を満足させるために、
複数の企業体が海外の技術提供を受けつつ、設計・製作・建設に従事した。
以下に各担当メーカー【技術提供会社】〔国名〕をまとめておく。
(発注元)住友石炭鉱業
@立坑掘削
別子建設梶@【フェルシャハト社】 〔ドイツ〕
Aスキップ巻上設備・立坑内/坑口坑底設備・櫓等
三菱造船梶@【グーテホフヌングスヒュッテ(GHH)社】 〔ドイツ〕
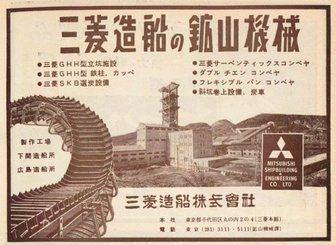
Bスキップ巻上設備 制御
活タ川電機製作所 【ブラウン・ボベリ(Brown, Boveri & Cie. 略称: BBC社】 〔スイス〕
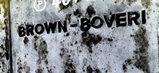
Cケージ巻上設備及び制御
富士電機梶@【「古河電気工業」と、ドイツの「シーメンス社」技術提携により設立】 〔日本〕
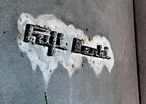
活タ川電機製作所とブラウン・ボベリの出会い
戦後、日本経済が安定してくるにつれて産業界が求めたのは、
生産性の向上で、電動機においてはより俊敏で精密な自動制御が求められていた。
当時、安川電機が供給していた商標であるVSモータ(交流AC)は、
「インバーター」モーターの回転速度を可変させるために、
交流→直流→交流などに変換させる装置
の無かった時代に、電磁石の力で定格回転のモーターの、
出力軸に力を加えて、回転数制御を行う画期的なものだった。
時代背景から精密な制御を求められた安川電機であったが、
大容量直流制御器の実績に乏しく危機感を持っていた。
当時の他国内重電機メーカーは家電への進出が盛んで、
安川電機としては他社との差別化のために、その特異性を維持する必要に迫られており、
直流(DC)機による自動制御技術の採用を模索していた。
そんな中、戦時中に技術的遅延が発生した日本の水準を克服するために、
スイスの重電メーカーとの技術提携は最適であるとされ、
期せずして昭和28年(1953)にブラウン・ボベリ社の常務の日本視察が執り行われる。
安川電機は社内工場見学を実施し、意見交換と技術提供を依頼した。
当時のブラウン・ボベリ社は技術の提供は行わず、
製品の輸出が目的であったが、実は国内の4社が技術提携を熱望している状況であった。
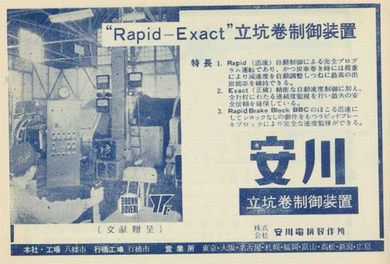
時代背景から抄紙機や鉄鋼圧延機、そして立坑巻上機への直流(DC)機自動制御技術についての分野で、
技術提携を希望しその折衝は8回に及ぶ。
通産省の許可や技術導入に伴う売上の相当額の製品を輸入するという条項などの、
多くの側面的な苦心も相まって、技術提携の合意に至った。
奔別立坑は日本初の多索式、つまりロープ複数(2本)による運転方式である。
一本索式
多索式(二本索式)
《利点》
・ロープ直径の小径化。
同荷重を吊る場合、単純にロープ数を増やせば1本吊の場合よりも小径ロープで良いこととなる。
例えば1本吊でφ80oのロープを必要とする場合、2本吊ならφ57o、4本吊ならφ40oで事足りることとなる。
ワイヤーロープ
ロープの小径化によって、製造工程上、不均一となりがちな大径ロープに比較して、ロープ品質の向上が期待できる。
また、ロープ内部の検査においても電気磁気的な装置が不要で外部からの素線の監視も容易である。
立坑内のロープ掛け変え交換作業においても、運転においても取り扱いが容易となる。
・滑車の小径化。
ロープの小径化が図れれば、必然的にヘッドシーブ(滑車)等も小径化が可能となる。
具体的には1本索の場合シーブ直径φ8.8mに対して、2本索とすればφ5.5mとなり、
さらに4本索とすれば約φ3.6mでよいこととなる。
・安全性の向上。
また、多索巻きであればすべてのロープが一度に切れることはなく、
もし、1本のロープが切断しても、他のロープにより保持されるので、
多索巻きの方が1本索に比較して安全率が高いと言える。
・スリップ率の低下。
しかも、ロープとプーリ/シーブの巻付け角と摩擦係数に追加して、
多索の各ロープの張力の差がお互いにスリップをけん制しあうことで、
摩擦が高められる二次的効果がある。
《短所》
ロープは張力により必然的に伸びが発生する。
しかも複数のロープが均一の伸びを示すことは無く、それぞれが単独の割合で伸縮する。
つまり時間経過とともに、複数のロープがそれぞれ異なった長さに変化することがある。
この長さの異なるロープそれぞれに、等荷重が掛かるように
「スキップ」地下で採掘した石炭を積込む箱及び
「ケージ」人員・炭車輸送用の箱
の上部に特殊な吊り金具を接続することで、これを対策する。
吊金具
三角形横梁型の吊金具下端をケージ(スキップ)の上部に取り付けることで、
三角梁の傾きにより、ロープ長の差を吸収でき、掛かる張力の不同が調整可能となる。
立坑内径の決定
立坑内径を決定する要素としては、炭車(トロッコ)の寸法、
ケージ・スキップ/立坑壁の相互間隔、風量などが考慮される。
炭車については従来の斜坑型から立坑型に改造するため、
ドイツのDIN規格を参考に容量2m3、長さ2.73m、幅0.97mのものが設計された。
ケージと立坑壁の間隔は剛性ガイドを使用する場合、
一般に150mmとされているが、中空クッションブロックを外巻壁に使用することで、
軟弱な地層に対応し、250oで計画された。
ここから立坑内径は6,400oと決定されたが、
その後坑内設備の変更により、ケージ/立坑壁間隔は230oに変更されている。
一方、通気計算では立坑有効断面積32m2(3.2m×3.2m×3.14)に対して、
立坑内諸設備を除いた有効断面積が28m2となり、
必要風量8,000m3/分として、平均風速は約320m/分となり、
これは妥当とされた。
築壁構造
立坑掘削部分は幌内層と呼ばれる軟弱な塑性岩盤であり、
これは立坑坑道に向かい、周囲の岩盤が滑り出してくる状況にある。
地盤の滑りは内部摩擦が多く、多くの時間を費やしながら発生することが予想され、
工事開始からの時間の経過と共に、立坑の内部応力は大きく変化する。
つまり掘削開始時は滑りの量が多く、地盤内の
「応力勾配」穴の周辺など力の集中する部分と分散する部分において力のかかる部分が一定でなく変化すること
は急激となる。
しかし時間の経過と共に、岩盤の滑り速度が遅緩になると、
立坑の坑壁にかかる荷重の増加速度も減少しやがてゼロとなる。
そのため塑性岩盤中の立坑築壁としては、強度と共に可縮性を求めることとなり、
本坑の場合は、内巻坑圧部と外巻可縮部の二重巻構造として、
強度管理と破損補修に優れたコンクリートブロック築壁を採用するに至った。
この理論をもって種々の検討の結果、
内巻には巻厚450oのA型ブロック、外巻には巻厚250oのコンクリートブロック、
(後にズリの焼屑中空ブロック)を用いることに決定した。
【立坑仕様】
立坑仕上内径:6.4m
堀鑿径:7.9m
堀鑿断面:49.0m2
仕上断面:32.2m2
壁厚:750o(内巻450o/外巻250o)
深度:735m(坑口標高+75L/坑底標高−660L)
連結部:−340L及び−550L
開墾設備
立坑の掘削には坑口上に仮の
「開墾用櫓」鉄骨構造 全高25.7m 底面10×13m 自重40t
を組んだ後、
「キブル」容量1.3m3 自重700s サイズ直径φ1,250o/高さ1,200o 3個使用
と呼ばれる下部に向かって掘削するときの破砕岩を搬出するバケツを用い、
これを
「ホビン巻上機」西ドイツ製365馬力 500V 395A 980rpm 11.5m/分 全長800m
を使用して搬出する。
立坑内部の掘削や巻壁の作業には、
「スカホード」直径6.25m 全高4.9m 3段デッキ式 自重10,460s
という円柱状の移動式足場を使い、
これを
「スカホード巻上機」単胴50kw 200v 600rpm 3段減速5m/分 ロープ径φ65o
を用いて上げ下げする。
スカホードの下部には
「グライファー」圧気動 ロープ径φ22mm ロープ速度0.32m/分
と呼ばれる小型ウインチがあり、ブロックや資材の搬入出に使用される。
その他付近で製造したブロックの搬入のために、「ブロック籠」自重232s ブロック53個積込可能
等が利用された。
ブロック製作
立坑のすぐ近隣には骨材工場、ブロック工場、ブロック貯蔵庫が隣接された。
ブロック工場で製作されたブロックは7種に及び、
密度や水との配合の違いにより成形され、
立坑内巻/外巻/フーチング/連接部/風井用など比重や強度が最適なものが製造された。
ブロック工場の人員は20〜25名で対応し、時間当たり60〜110個の成型が可能であった。
ブロック貯蔵養生室のキャパシティは2,640〜3,072個ということで、
1日当たりの製造数に制約をもたらす状況となった。
@電動機速度制御の必要性
立坑の巻上機(=モーター)はロープを用いた運搬機器であり、
大馬力・運搬距離が長い・高速・ロープ自重の影響・使用目的による速度制限などの諸条件や、
坑底⇒坑口⇒坑底と移動する際に、臨機な速度変化が必要となる。
つまりスタートは低速、徐々に加速して短時間で最高速に達した後、
ある深さで減速し、微速となり停止する。
この一連の加速度変化が要求される以上に、実は重要な速度制御が求められる。
その理由は前述の
「デッキチェンジ」トロッコをケージと呼ばれるエレベーター箱から積み降ろしする作業
の存在である。
人員の乗り降りは多少の段差があっても問題ないが、
レイルを介したトロッコにとっては、小さな段差も乗り越えられず、
ケージと軌道面の着床位置が非常に重要となる。
そして1ケージに3台のトロッコが積載される場合があり、
その時には微速⇒停止⇒微速の一連のステップを3回繰り返すこととなる。
着床精度が悪いことは、鉱車(トロッコ)の入替に非常に不便となり、
場合によっては再度停止位置調整が必要となり、非効率この上ない。
着床精度は停止前の速度が低いほど、また安定しているほど良好である。
しかし運搬能率上からは、微速度が低く、微速運転時間が少ないほうが良い。
通常、停止前速度は0.4〜0.9m/s程度が要求され、これは全速の1/10以下の速度の安定が必要となる。
現実の要求着床誤差は750mの中の±18oと言われる。
A直流と交流
電気とはエネルギー形態の一つで、+と−の極性があり、
電気的性質を持った電荷というものが移動することで起こる現象だ。
基本、+側から−側に電気が流れ、流れる強さを
「電圧」記号E 単位【V】ボルト
一定時間に流れる量を
「電流」記号I 単位【A】アンペア
という。
電流の大きさは両極を繋ぐ
「導体」電気が流れる物質
の電気の流れにくさで決まる。
これは
「電気抵抗」記号R 単位【Ω】オーム
と呼ばれ、
電気抵抗が高い(=流れにくい)ほど同じ電圧でも電流は小さくなる。
これが
「オームの法則」E(V)=R(Ω)×I(A)
で大きな抵抗がかかる部分にたくさんの電流を流したいときには、掛ける電圧を大きくすれば良い。
乾電池には+と−があるが、家庭用のコンセントには+と−が無い。
これは流れている電気の種類が違うからだ。
自動車の12Vや乾電池など一方通行の「直流」DC=direct current
は流れる方向と電圧が一定の電流のことだ。
一方、家庭用100Vなどの「交流」AC=alternating current
とは流れる方向と電圧が周期的に変化する電流であり、
遠くまで送電するのに必要な
数万〜数十万Vという高い電圧を発生させやすく、使用時に簡単に電圧を下げることができる。
1秒間に電流の流れる向きが何度変わるかは周波数と呼ばれ
「Hz(ヘルツ)」かつてはc/s サイクル毎秒 (cycle(s) per second)
という単位を使用する。
日本国内では過去に導入した発電機の違いを発端に、静岡〜新潟間を境界に西側は60Hz、東側は50Hzが使用されている。
つまり1分間に西日本は60回、東日本は50回、+と-が入れ替わり、この
「サイクル」東日本50Hz 3000rpm回転のモーターは西日本60Hzで3600rpm回転する
でモーターの回転数も固定される。
奔別立坑 昭和36年
従来、大型立坑巻上機は直流DC方式が主流であった。
当時、交流ACは小型巻上機に限られていたが、昭和29年に低周波制御が発明され、
その後、交流ACの進出が目覚ましくなった。
直流DCが優位な点は、エネルギー損失が小、回生エネルギーが流用できる、負荷に左右されない速度制御が可能と、
何よりそのトルク(力)と制御の簡易性が大きかった。
ところがそれを克服する、減速機の誕生が起こる。
それまでと違い、高精度で経済的に減速機が作製されるにあたり、昭和35年以降、その交流ACの弱点が克服されつつあった。
そのように交流ACが要求される理由は主にコストだ。
交流ACは直流DCの約半値と言われる。ただしこれは立坑運搬設備全体から見れば5%のことである。
深度と出炭量の関係を加味しても、この時代はまだまだ直流DCの優位性には対抗できなかったようだ。
その中でのケージ側の交流ACへのチャレンジは特筆するものがある。
奔別立坑の左右ではほぼシンメトリーに巻上システムが存在し、前述したとおりそれぞれメーカー及び制御が相違していた。
そしてその違いは驚くべきことに、メーカー及び制御に留まらず、
交流(左=ケージ側)・直流(右=スキップ側)とその回路を構成する基本要素からして異なっていたのだ。
マウスon
写真提供は
fall_125様
B立坑における直流巻上機と交流巻上機
ケージやスキップを巻き上げるためには、そのロープを巻き取る
「ケーペプーリ」動力滑車
を駆動する必要がある。
そのためには電動機(モーター)を稼働させることとなる。
交流AC電動機(モーター)は ブラシ が不要で単純構造、故障が少ないが、基本、回転数の調整ができない。
直流DC電動機(モーター)は小型高出力、電源電圧を変えるだけで回転数を自在に可変可能。 交流に対しては高価、外力により回転数変化が発生する。
前述のとおり着床精度のための微速コントロール、最高速区間への効率的な加速など
立坑巻上機はシビアな回転速度の制御が求められ、現在のように
「インバータ」交流モーターの回転速度制御を電源周波数を変化させることで行う
が無い時代、それでも当時の最新技術を用いて制御を行っていた。
ケージ側制御について
向かって左手、人員・トロッコを積載するケージを運転していた
富士電機側は交流ACによる制御であった。
交流の回転数制御は電源周波数を変化させることで
「同期速度」発電機と電動機の回転速度のズレで減速、加速を行う
が変わるので、
これを用いて誘導モーターの回転速度を変化させる。
これは『ACギヤ減速式 低周波制御方式』と呼ばれ、具体的には、通常50c/sの巻線型
「三相」同じ周波数で同じ電圧の3組の単相交流が周期1/3づつずれた状態でまとまっている
電動機で稼働し、
ある深度からの減速低速域区間では2.5c/sの低周波制御用発電機に切替えて駆動する。
交流モーターの回転数は
「電源周波数」西日本は60Hz、東日本は50Hz
に同期しているため、減速(電気的に回転数を落とす)するためには、
ヘルツ(=c/s)を落とさなければならない。
そのために
「励磁機」コイルに電流を流して磁界を作る装置
で整流され、周波数を落とした発電機に切替えて、
その早い回転のメイン電動機と遅い回転の発電機の回転数差をブレーキングとして、
減速効果を導くのである。
ACモーター
スキップ側制御について
一方、向かって右手、石炭・ズリを積載するスキップを運転していた
活タ川電機製作所側は直流DCによる制御であった。
直流の回転数制御については
羽幌運搬立坑と同様の『ワードレオナード方式』であった。
これは交流電動機(モーター)で直流発電機を定格駆動、その発電機を
「界磁制御」磁石で磁界をコントロールし抵抗制御を行う。
し、
その変化した直流電源を用いて直流電動機(モーター)を稼働しスピードコントロールする方式だ。
具体的には、一旦交流三相の商用電源(外部からの電源)を用いて、一定速度で交流モーターを駆動する。
それにシャフトで接続した直流発電機を定格で回し、DCの発電を行う。
その発生した直流(DC)電源を磁力で強弱し、そのコントロール可能となった電源を用いて、
ケーペプーリに直結した、直流モーターの回転数制御を行う。
DCモーター
坑底切羽からの石炭を炭車に積込んで、炭車のまま坑口へ揚げる
「ケージ」人員・炭車輸送用の箱方式と
坑底立坑付近で転車した石炭をバラ積みして坑口で流す
「スキップ」地下で採掘した石炭を積込む箱方式の
選定はどのように行われていたのだろうか。
スキップは設備の関係上、トロッコから坑底転車・
「メジャリングバンカ」転回したトロッコからスキップまでの石炭積込装置
投入時・スキップ石炭流入時・坑口排出時と計4回の粉化の機会があり、
このうち最もその落差が大きいものが、メジャリングバンカからスキップへの投入時となる。
スキップによる粉化においての炭価下落と、自動運転の容易性、時間当たり積載量の大きさなど、
その短所と利点の比較を検討してみよう。
運炭を主とすれば、ケージ/スキップとも同一量の石炭の積載が可能と考えられ、
その積載総重量は同様の8tと考える。全速を12m/s、運搬距離を700/750mとすると、
その運航時間はスキップ74.5秒、ケージ70.4秒となる。
ケージの押し込み時間8秒、デッキ交換6秒とするとそれらを加味したサイクル時間は、
それぞれ87.5秒/70.4秒となり、そこから時間当たりの運搬量を算出すると、
スキップによる運炭がケージの137%となり、粉化さえ考慮すればスキップの方が優位という結果となる。
ケージ
立坑巻上機は一般機械とはかなり異なった性質を伴っている。
巻上工程毎回1秒のロスは、年間1〜2%の出炭減になると言われ、能率上以下の内容が要求される。
@運転のスピードアップ
A容量の増大
B事故の皆無
C容易な運転
D精密着床、デッキチェンジ等特殊運転の効率化
現在ならその制御は
「シーケンス」対象物の状態が目標値であるかをセンサで
確認しながら、一連の手順に従って工程を進めていく
を用いて連続的に行われるはずだが、当時はまだその技術がなかった。
最大の出炭量をあげるために、加速度及び減速度を増大した上で能率的なプログラム運転が必要である。
特に
「ケーペ式」ドラムにロープを巻き取らず、
ヤジロベーのようにロープ両端で交互に地上と坑底を結ぶ
の場合は急激な動作を避け、ロープスリップを防止する。
また、着床とデッキチェンジのために必要な
「低速度」0.3m/sec程度でこれは全速の1/70
を確実に得られ、かつ加速・減速電流の最高値が常に許容範囲内でなければならない。
それでいて何よりもの安全性の確保である。
操作盤
目標は経済性をも考慮した無人の完全自動化運転であるが、
当時設備化されたのは、遠隔操作による有人の自動化運転であった。
無人自動化運転が困難な理由としては以下がある。
使用ロープの時間的な伸びがあり、積載荷重の変動による着床の誤差が大きかった。
スキップの場合は坑底積込シュートと坑口排出シュートのスキップ開口部との位置に、
十分余裕をとれば、自動運転もそれほど困難ではない。
ところが、ケージ側においては、人員搭乗、炭車積載など一定量とはならない重量が悪影響となり、
また、車輪抵抗や変形など個体差のある2t以上の炭車の停止・起動も監視者の必要性を高めている。
しかし、奔別立坑においては巨大な深度計が姿を消し、自動スリップ調整器など当時最新の設備が惜しみなく投入され、
特にスキップ側の運転は釦による1サイクル自動式となり、
デスク型操作台の運転手はほとんど監視だけの作業となっていた。
それに対してケージ側は複雑な複数レバー式での運転であり、
一定深度を通達するベルにより、オペレーターは減速作業を施し、
万が一の場合は非常ブレーキが作動する機構であった。
ケージ側(富士電機梶j
スキップ側(ブラウンボベリ社)
立坑左右での相違点
ケージ側(左) |
スキップ側(右) |
富士電機(日本) |
ブラウンボベリ(スイス) |
交流(AC) |
直流(DC) |
減速機あり |
減速機なし(直結) |
低周波制御 |
ワードレオナード制御 |
ケーペプーリ穴密閉 |
ケーペプーリ穴有 |
手動運転 |
半自動運転 |
A立坑櫓メインへ
奔別立坑へ戻る
B(左)ケージ側
C(右)スキップ側